Pulver, Folie und Granulat in Popcornform
07:33 Minuten
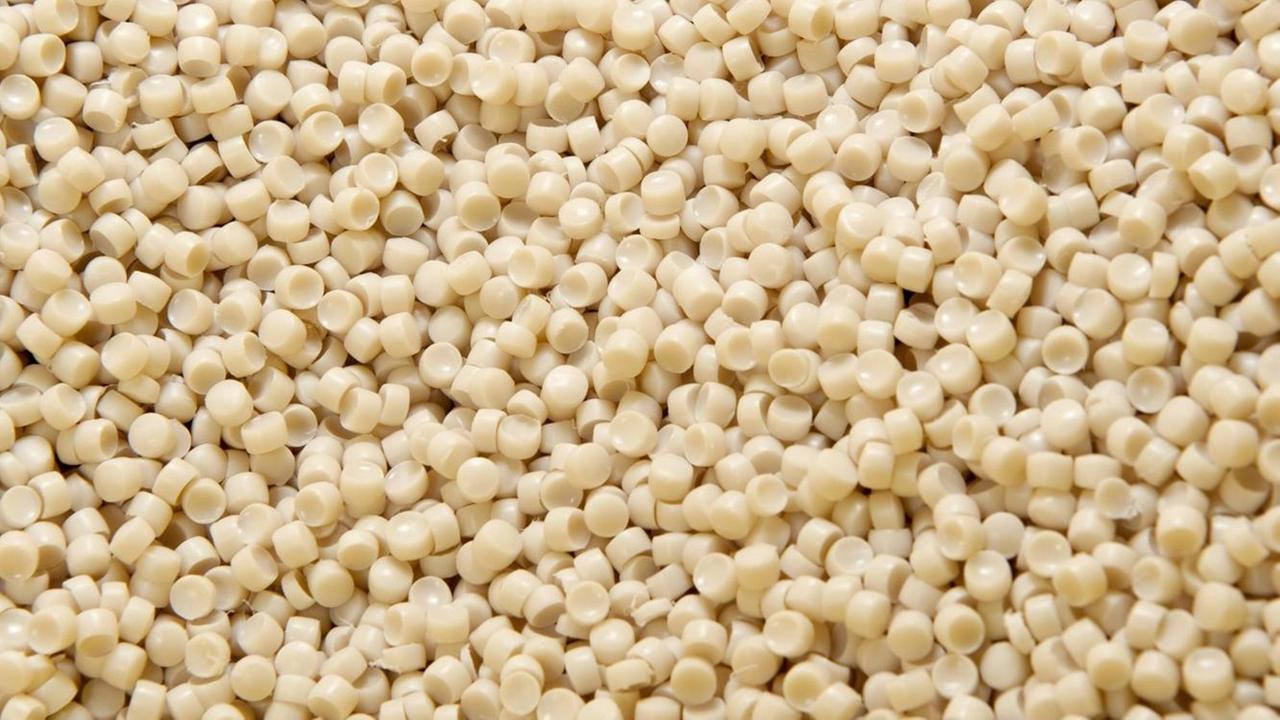
Fast alle Kunststoffe werden aus fossilen Rohstoffen hergestellt. Aber das Bewusstsein für Alternativen wächst. Allerdings sind "Biokunststoffe" auch nicht per se umweltfreundlich. Ein Forschungsprojekt unter Mitarbeit der TU Berlin will das ändern.
Sebastian Riedel führt durch eine große Halle eines Backsteingebäudes der TU Berlin. Labortische, Regale, Versuchsapparaturen stehen in dem lichtdurchfluteten Raum. Die Lüftung surrt. Zwei Doktoranden bauen eine Apparatur ab, ziehen Kabel, die zu einem mannshohen Stahltank führen: einem Bio-Reaktor mit 100 Litern Arbeitsvolumen.
Er spielte in einem vor kurzem beendeten Versuch eine zentrale Rolle. Sebastian Riedel, Arbeitsgruppenleiter des Bereichs Bioverfahrenstechnik, zückt sein Handy. "Hier ist ein Foto des Reaktors mit Studententeam. Da läuft der Reaktor. 746 Likes."
Das war ein erfolgreicher Durchlauf, sagt Sebastian Riedel und stellt eine Glasflasche mit blauem Schraubdeckel auf den Tisch. Er zeigt, wie die Ernte des Versuchs aussieht.
Bakterien im Hungerstress
"Das ist die Biomasse. So ein getrockneter Hefewürfel, so sieht das aus", sagt er. Die Biomasse sind gefriergetrocknete Bakterien der Gattung Cupriavidus necator, einem sehr verbreiteten Bodenbakterium.
Zu Beginn des Versuchs, erklärt Sebastian Riedel, gehe es ihnen hier in der Anlage besser als in der Natur – unter anderem hätten sie Nahrung im Überfluss. Dann aber werde die zum Wachsen wichtige Stickstoff-Zufuhr gekappt – das setzt die Bakterien künstlich unter Hungerstress.
"Und dann, wenn wir weiter Kohlenstoff hinzufüttern in Form von tierischen Fetten oder pflanzlichen Fetten, speichern sie den überschüssigen Kohlenstoff als Energiespeicher ein. Das ist ein linearer Polyester und der hat ähnliche Eigenschaften wie herkömmlich basiertes Plastik", erzählt er.
Kunststoff aus Fettabfall vom Schlachthof
Gefüttert hat Sebastian Riedel knapp sechs Kilogramm Alt-Fett, das von Schlachthöfen kommt und außer zur Verbrennung nicht weiter benötigt wird. Innerhalb von ungefähr drei Tagen haben die Bakterien dieses Fett verwertet und dreieinhalb Kilogramm Bio-Kunststoff gebildet.
Um die größtmögliche Menge an Biokunststoff zu erhalten – die maximale Ausbeute – ist es für den Verfahrenstechniker wichtig, den genauen Zeitpunkt für die Ernte zu kennen. Also: den Punkt, an dem der Versuch im Bio-Reaktor gestoppt wird und die Bakterien im Istzustand verbleiben.
Doch den zu ermitteln, ist nicht ganz einfach: "Was man bisher nicht messen konnte, ist die Anreicherung des Bioplastiks in der Zelle. Sie können sich also vorstellen, dass die Zellen – ich sag jetzt mal der Einfachheit halber Kügelchen – die lagern das Plastik in Kugelform innerhalb der Zelle an", erklärt Sebastian Riedel.
"Und sozusagen, während der Prozess im Reaktor läuft, in die Zellen reinzuschauen und zu schauen, wie viele von den Plastikkügelchen haben wir und wie groß werden die – das war bisher nicht möglich."
Vollständig biologisch abbaubar
Thomas Schiewe, Bioprozess-Ingenieur am Potsdamer Zentrum für Innovationskompetenz verwendet deshalb ein dort entwickeltes Messverfahren: Die Photonendichtewellen-Spektroskopie, die es ermöglicht, die Vorgänge in den Zellen in Echtzeit zu beobachten. So konnten die Forscher in Kooperation mit der TU Berlin ermitteln, dass die Bakterien im Bio-Reaktor die maximale Kunststoff-Menge nach 72 Stunden gebildet hatten.
Nach dieser Zeit allerdings befindet sich der Stoff – Polyhydroxyalkanoat, kurz: PHA – noch in den Zellen und muss herausgelöst werden. Sebastian Riedel stellt drei Flaschen auf den Tisch.
"Je nachdem, wie wir das machen, bekommen wir so ein ganz feinkörniges Granulat, hier ein gröberes zusammengekrümmt, das sieht so ein bisschen aus wie Popcorn, sagen manche. Oder auch schon eine Folie. Das Besondere am PHA ist, das wird aus biogenen Reststoffen hergestellt von den Mikroorganismen und kann dann auch wieder von Mikroorganismen abgebaut werden", erläutert er.
"Wie normales Plastik auch, degradiert es auch und wird irgendwann bröselig, zerbricht und wird immer kleiner, aber dadurch, dass es eben abgebaut wird, entsteht kein Mikroplastik. Unter aeroben Bedingungen entsteht CO2 und Wasser, so wie es entstanden ist. Es ist dann komplett weg."
Hohe Plastiknachfrage während der Pandemie
400 Millionen Tonnen Kunststoff werden weltweit jährlich produziert, die meisten aus erdölbasierten Rohstoffen. Der Anteil von Biokunststoffen – ob biologisch abbaubar oder beständig – liegt derzeit nur bei etwa einem Prozent. Verschwindend gering und daher eine Chance für Biokunststoffe, auch vor dem Hintergrund der Corona-Pandemie, in der die Nachfrage nach Kunststoffen enorm gestiegen ist.
"Gerade im Rahmen des Gesundheitsschutzes und der Hygiene sind die Kunststoffe wieder salonfähig geworden. Im Prinzip kann man sagen, das hätte wahrscheinlich keine PR-Kampagne so erfolgreich geschafft und das heißt natürlich auch, dass mehr Biokunststoffe eingesetzt werden können", sagt Lisa Mundzeck vom Institut für Biokunststoffe und Bioverbundwerkstoffe an der Hochschule Hannover.
Auch ein Biokunststoff muss auf seine Nachhaltigkeit geprüft werden und für eine aussagekräftige Bewertung ist eine detaillierte Ökobilanz erforderlich. Und auch bei Bio-Plastik ist die oft besser, wenn es wiederverwendet werden könne.
Bio ist nicht gleich Bio
Das ist bei Sebastian Riedels PHA nicht der Fall, Abbaubarkeit hin oder her. Allerdings, sagt Lisa Mundzeck: Es gibt Anwendungsgebiete, bei denen die Einmalnutzung sinnvoll erscheint.
"Bei den Abbaubaren ist es eigentlich so, dass wir am IFBB die Meinung vertreten, dass man die Abbaubaren tatsächlich nur da einsetzen sollte, wo der Charakter der Abbaubarkeit wirklich einen Zusatznutzen ergibt. Also zum Beispiel, wenn man an Mulchfolien in der Landwirtschaft denkt, wo man tatsächlich auch Geld und Zeit spart, wenn der Landwirt diese Folien einfach unterpflügen kann", sagt sie.
Sebastian Riedel hat – unter anderem – genau solche Folien vor Augen, wenn er an die Anwendungsmöglichkeiten seines Verfahrens denkt. Zudem hofft er, dass er die entstehenden Mengen noch steigern kann.
"Dass wir die verschiedenen Kohlenstoffquellen, also die verschiedenen organischen Abfälle wie tierische Fette oder Protein-Fett-Gemische, pflanzlichen Abfallfette oder Zuckerreste, dass man die verschiedensten Ausgangsreststoffe nutzen kann und das gewünschte Polymer in einer großen Menge herstellen kann", erklärt er.
Ein Kunststoff aus biogenen Reststoffen, der selbst wiederum komplett abbaubar oder recycelbar ist – das wäre tatsächlich ein geschlossener nachhaltiger Kreislauf.