Maschinen lernen denken
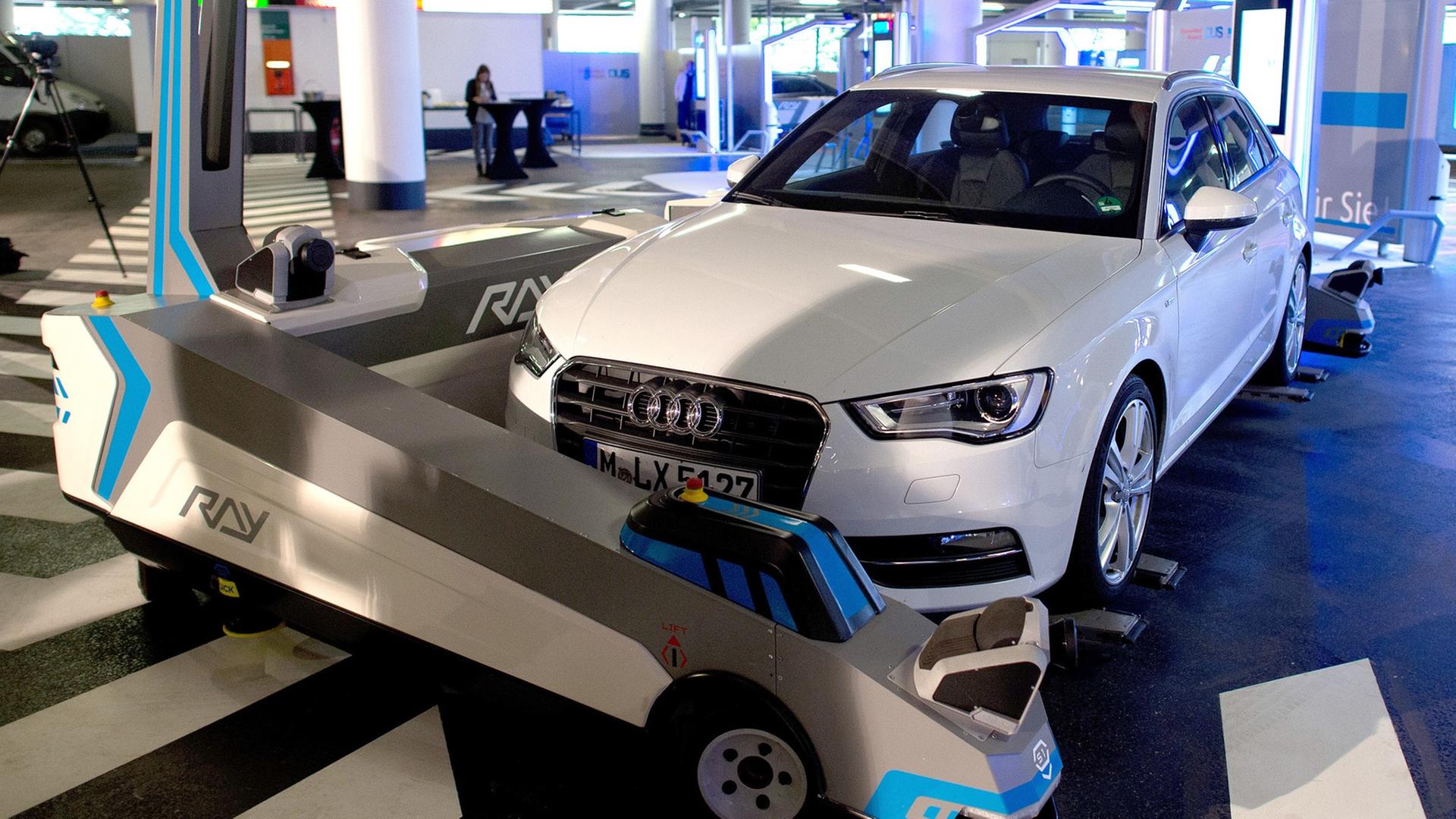
Selbst der Industrieroboter erlebt die Evolution, eine digitale Evolution. Er soll künftig nicht einfach nur anheben oder Hitze aushalten, sondern planen und kommunizieren. Die neuen Roboter übernehmen sogar Verantwortung.
Mit einer leichten Handbewegung hat Christiane Bösl den Roboter im Glasgehäuse wieder in Bewegung gesetzt.
"Ich kann den Roboter zum Laufen bringen. So weit geht's!"
Mit seinem Greifer positioniert er ein zentimetergroßes Bauteil millimetergenau auf die dafür vorgesehene Stelle auf der Leiterplatte. Von oben senkt sich der Druckzylinder und presst es fest. Während er wieder hochfährt, hat der Roboter schon das nächste Stück für die nächste Leiterplatte im Griff und setzt es mit leichtem Zischen ab.
Jeder Arbeitsschritt wird datentechnisch in Echtzeit erfasst. Die reale Produktionswelt wird im laufenden Betrieb eins zu eins virtuell abgebildet. Werksleiter Karl-Heinz Büttner kann jederzeit einzelne Produktionsvorgänge am Bildschirm aufrufen.
"Alle unsere Maschinen sind online: Der Bestücker, der Drucker, der Ofen ist online, sodass wir mit den Maschinen kommunizieren können. D.h. Maschinen können uns sagen, was sie gerade tun und wir können den Maschinen sagen, was sie zu tun haben. Und über diesen Weg sind wir in der Lage mit allen Bestandteilen unserer Fertigung ständig online zu kommunizieren und zu steuern."
Jeder Arbeitsschritt wird datentechnisch in Echtzeit erfasst. Die reale Produktionswelt wird im laufenden Betrieb eins zu eins virtuell abgebildet. Werksleiter Karl-Heinz Büttner kann jederzeit einzelne Produktionsvorgänge am Bildschirm aufrufen.
"Alle unsere Maschinen sind online: Der Bestücker, der Drucker, der Ofen ist online, sodass wir mit den Maschinen kommunizieren können. D.h. Maschinen können uns sagen, was sie gerade tun und wir können den Maschinen sagen, was sie zu tun haben. Und über diesen Weg sind wir in der Lage mit allen Bestandteilen unserer Fertigung ständig online zu kommunizieren und zu steuern."
"Wenn wir sagen, dass unsere Maschinen online sind, dann heißt das, sie sind in einem eigenen Produktionsnetz, was natürlich geschützt ist. Wir haben im internen Netz ähnliche Verhältnisse wie im Internet. Wir haben auf alles Zugriff. Jede Maschine ist erreichbar und jede Maschine kann sich melden, wenn Bedarf da ist."
Das EWA, das Elektronikwerk Amberg in der Oberpfalz, gehört zu Siemens und stellt die Steuerungseinheit Simatic her. Mit ihr werden Fließbandstraßen im Automobilbau, Abfüllanlagen von Brauereien oder Verpackungsanlagen in der pharmazeutischen Industrie gesteuert.
Das EWA gilt mit seinem gegenwärtigen Stand der Automatisierung und Digitalisierung als die modernste Fabrik Europas. Besucher aus der ganzen Welt kommen hierher, um sich von Effizienz und Optimierungspotenzialen der "digitalen Fabrik" ein eigenes Bild zu machen.
Als die Weber auf die Barrikaden gingen gegen Webstühle, die nicht mehr von Hand, sondern von Maschinen angetrieben wurden, kämpften sie gegen Ausbeutung und Rechtlosigkeit. Die industrielle Revolution im 19. Jahrhundert war auch ein gesellschaftlicher Umbruch. Ähnliches steht uns, wenn wir den Versprechen der Industrie glauben auch bevor. Deshalb haben sie sich ein "Punkt Null" gegönnt.
Das EWA, das Elektronikwerk Amberg in der Oberpfalz, gehört zu Siemens und stellt die Steuerungseinheit Simatic her. Mit ihr werden Fließbandstraßen im Automobilbau, Abfüllanlagen von Brauereien oder Verpackungsanlagen in der pharmazeutischen Industrie gesteuert.
Das EWA gilt mit seinem gegenwärtigen Stand der Automatisierung und Digitalisierung als die modernste Fabrik Europas. Besucher aus der ganzen Welt kommen hierher, um sich von Effizienz und Optimierungspotenzialen der "digitalen Fabrik" ein eigenes Bild zu machen.
Als die Weber auf die Barrikaden gingen gegen Webstühle, die nicht mehr von Hand, sondern von Maschinen angetrieben wurden, kämpften sie gegen Ausbeutung und Rechtlosigkeit. Die industrielle Revolution im 19. Jahrhundert war auch ein gesellschaftlicher Umbruch. Ähnliches steht uns, wenn wir den Versprechen der Industrie glauben auch bevor. Deshalb haben sie sich ein "Punkt Null" gegönnt.
Die vierte Stufe der industiellen Revolution
Vor drei Jahren kreierten Experten des High Tech Forums der Bundesregierung den Begriff "Industrie 4.0". In ihrer Zeitrechnung beginnt die Industrialisierung mit der Dampfmaschine, ihr folgt die Elektrifizierung und Taylorisierung, dann die Automatisierung und Einführung von Robotern. Mit der Vernetzung der Maschinen in Echtzeit ist für sie eine vierte Stufe der industriellen Revolution erreicht. Der Begriff "Industrie 4.0" beschreibt eine Zukunftsvision und soll gleichzeitig Marketing sein; eine griffige Formel für das Neue, das sich gegenwärtig hinter Fabrikmauern vollzieht.
Von Außen erweckt das Elektronikwerk Amberg nicht den Eindruck einer Hightech-Fabrik. Siemens hat das Werk 1989 gebaut, im Laufe der Jahre erweitert ... und parallel zur realen Produktion ein virtuelles Abbild geschaffen.
Am Eingang zur Maschinenhalle zeigen Monitore die aktuellen Produktionsdaten an. Einer davon: 0,4 dpm. Dpm ist eine Maßeinheit für die Fehlerquote in der Produktion und heißt so viel wie: Defekte pro einer Million von Möglichkeiten! Durchschnittlich werden einer guten Arbeitskraft 500 dpm zugeschrieben. Mit der Datenanalyse aus der Produktion, an die 50 Millionen Daten fallen täglich an, werden die Abläufe ständig kontrolliert und neue Möglichkeiten der Optimierung entwickelt, erklärt Werksleiter Karl-Heinz Büttner. Der promovierte Informationstechniker kam von Zeiss Jena zu Siemens. Für den Konzern war er in den USA und China und ist jetzt seit fünf Jahren in der Oberpfalz.
"Digitalisierung bedeutet für mich, für uns: Jedes Ding in der Fertigung hat einen Namen, bei uns einen Barcode und jeder Prozessparameter wird gemessen. Und so erhält jedes Ding seine Geschichte, wie es verarbeitet wurde. Und deshalb wissen wir für jedes Produkt, wann es produziert wurde und können in Fehlerfällen nachvollziehen, was passiert ist und sehen, wie wir es verbessern können."
So beginnt der Fertigungsprozess der Steuerungseinheit: Eine Arbeiterin legt die vorgefertigte grüne Leiterplatte aufs Band, die Maschine zieht sie ein und druckt den Barcode auf; einzigartig wie eine DNA ist damit jedes Produkt identifizierbar in seinem zukünftigen "Lebenslauf".
Am Eingang zur Maschinenhalle zeigen Monitore die aktuellen Produktionsdaten an. Einer davon: 0,4 dpm. Dpm ist eine Maßeinheit für die Fehlerquote in der Produktion und heißt so viel wie: Defekte pro einer Million von Möglichkeiten! Durchschnittlich werden einer guten Arbeitskraft 500 dpm zugeschrieben. Mit der Datenanalyse aus der Produktion, an die 50 Millionen Daten fallen täglich an, werden die Abläufe ständig kontrolliert und neue Möglichkeiten der Optimierung entwickelt, erklärt Werksleiter Karl-Heinz Büttner. Der promovierte Informationstechniker kam von Zeiss Jena zu Siemens. Für den Konzern war er in den USA und China und ist jetzt seit fünf Jahren in der Oberpfalz.
"Digitalisierung bedeutet für mich, für uns: Jedes Ding in der Fertigung hat einen Namen, bei uns einen Barcode und jeder Prozessparameter wird gemessen. Und so erhält jedes Ding seine Geschichte, wie es verarbeitet wurde. Und deshalb wissen wir für jedes Produkt, wann es produziert wurde und können in Fehlerfällen nachvollziehen, was passiert ist und sehen, wie wir es verbessern können."
So beginnt der Fertigungsprozess der Steuerungseinheit: Eine Arbeiterin legt die vorgefertigte grüne Leiterplatte aufs Band, die Maschine zieht sie ein und druckt den Barcode auf; einzigartig wie eine DNA ist damit jedes Produkt identifizierbar in seinem zukünftigen "Lebenslauf".
"Für jedes Produkt gibt es einen so genannten Arbeitsplan. In dem Arbeitsplan legt der Mensch fest, wie das Produkt produziert ist und über den Arbeitsplan wird unsere Halle für jedes Produkt gesteuert und damit weiß jedes Produkt wie und wann und wo es zu sein hat, um produziert zu werden."
Es liegt in der Logik dieser Prozesse, erklärt Karl-Heinz Büttner weiter, dass Produkte und Maschinen sich künftig auch selbst organisieren.
"Unsere Struktur in der digitalen Fabrik ist so, dass wir auf der untersten Ebene schon Maschinen und Rechner entscheiden lassen, was zu tun ist. Und der Mensch entscheidet, welcher Rechner das darf. Erst wenn diese Entscheidungskompetenz überschritten ist, wird der Mensch informiert, der Mitarbeiter, um Entscheidungen zu treffen."
Das kann in diesen hochkomplexen Produktionsabläufen auch ganz einfach sein. Christiane Bösl weiß aus Erfahrung, wo es haken könnte, wenn die Roboter an ihrem Arbeitsplatz nicht mehr wollen.
"Das Förderband war voll und wenn die Lichtschranke versperrt ist, dann geht's nicht mehr."
Insgesamt beschäftigt das EWA tausend Mitarbeiter, die Hälfte davon sind Angelernte, darunter viele Frauen. Sie füttern die Maschinen mit Material, beaufsichtigen, prüfen.
Es liegt in der Logik dieser Prozesse, erklärt Karl-Heinz Büttner weiter, dass Produkte und Maschinen sich künftig auch selbst organisieren.
"Unsere Struktur in der digitalen Fabrik ist so, dass wir auf der untersten Ebene schon Maschinen und Rechner entscheiden lassen, was zu tun ist. Und der Mensch entscheidet, welcher Rechner das darf. Erst wenn diese Entscheidungskompetenz überschritten ist, wird der Mensch informiert, der Mitarbeiter, um Entscheidungen zu treffen."
Das kann in diesen hochkomplexen Produktionsabläufen auch ganz einfach sein. Christiane Bösl weiß aus Erfahrung, wo es haken könnte, wenn die Roboter an ihrem Arbeitsplatz nicht mehr wollen.
"Das Förderband war voll und wenn die Lichtschranke versperrt ist, dann geht's nicht mehr."
Insgesamt beschäftigt das EWA tausend Mitarbeiter, die Hälfte davon sind Angelernte, darunter viele Frauen. Sie füttern die Maschinen mit Material, beaufsichtigen, prüfen.
Suche nach Antworten für die Zukunft
"Man wird automatisch angelernt. Einen richtigen Beruf habe ich nicht gelernt."
Es liegt auf der Hand, dass in Zukunft die Arbeitsplätze von Angelernten weiter automatisiert werden und für die Schnittstellen zwischen realer und virtueller Produktionswelt höhere Qualifikationen gefragt sind.
Hartmut Hirsch-Kreinsen, Professor für Wirtschafts- und Industriesoziologe an der TU Dortmund, wurde in den wissenschaftlichen Beirat der Plattform Industrie 4.0 berufen, einem Zusammenschluss von Industrieverbänden der Elektrotechnik, des Maschinenbaus, der Informationswirtschaft und Telekommunikation. Er befasst sich mit Fragen der Zukunft der Arbeitswelt.
"In der Innovationsforschung kann man das als "disruptive innovation" bezeichnen. Konsequenzen, die jetzt nicht hundertprozentig übersehbar sind, die aber deutliche Strukturveränderungen - im Hinblick auf Technik, auf Organisation, aber auch im Hinblick auf Personal, nach sich ziehen. Und das hat zur Konsequenz, dass die disruptiven Innovationen auch ihre eigenen Widersprüche mittransportieren. Es ist teuer. Der Aufwand ist immens. Allein die Datenbestände anzugleichen, Datenbestände zu portieren! Das ist kein Prozess, den man von heute auf morgen lösen kann."
Im Industriegebiet von Pleidelsheim, auf der grünen Wiese und gleichzeitig strategisch an der A81 im Einzugsbereich der Automobilindustrie im Raum Stuttgart gelegen, montiert das mittelständische Unternehmen Zoller Messgeräte für den Maschinenbau, auch "zerspanende Industrie" genannt. Nach außen: Kein High-Tech-Image, sondern schwäbische Gediegenheit.
Als mittelständisches Unternehmen hat Zoller den aufwendigen Schritt in die Digitalisierung seiner Fertigung vollzogen.
Jedes einzelne Teil, das Michael Staib in das Gehäuse vor ihm einsetzt, hat eine IP Adresse. Entweder wurde es so schon angeliefert oder erhält im Werk eine Kennung. Ob ein bestimmtes Werkstück im Lager oder schon verbaut ist, das ist jederzeit und überall online abrufbar. Nachdem die Unternehmensorganisation und -planung mit ERP Systemen, Enterprise Planning Systems, durchdrungen wurde, folgt jetzt die Produktionswelt, das Internet der Dinge. Michael Staib, die Haare hinten zum Pferdeschwanz gebunden, die Arme tätowiert, ist von Beruf eigentlich Kraftfahrzeugmechaniker. Ein festes Berufsbild für seinen Arbeitsplatz gibt es noch nicht.
"Hierfür braucht es schon ein ordentliches Brain. Sie haben hier alles: Sie haben Elektrik, Sie haben Pneumatik, Sie haben Software, Sie haben Ultragenauigkeit und Sie müssen handwerklich unglaublich geschickt sein. Wir schreiben immer 3 Stellen hinter Null. D.h. ich setze dieses Gerät mechanisch im Tausendstelbereich zusammen. Und dann gehe ich mit der Software noch mal drüber, damit der Kunde wirklich im optimalen My-Bereich messen kann."
Wenn er alle Teile verbaut hat, überprüft er alles am Bildschirm. Erst nach einem virtuellen Probelauf, folgt der reale Testlauf. Die Digitalisierung der Arbeitsabläufe war für den Messgerätehersteller Zoller ein notwendiger Schritt, um konkurrenzfähig zu bleiben, erklärt Vertriebsleiter Bernd Schwennig.
"Es ist wichtig, dass insbesondere die zerspanende Industrie, die arbeitsintensiv ist, so gestaltet wird, dass diese Arbeitsplätze auch in Deutschland erhalten bleiben und der Mittelstand zusammenarbeitet, gemeinsam versucht vorhandene Verbesserungspotentiale so zu optimieren, damit auch in 10, 20 Jahren der Fertigungsstandort Deutschland noch attraktiv ist. Wir sind in der Lage mit der ganzen Welt zu konkurrieren und in Deutschland teilweise kostengünstig zu produzieren als in China."
Messgeräte für den Transport nach Übersee, in die USA, und eben auch China, stehen, in großen Holzkisten verpackt, bereit. Das Unternehmen aus Pleidelsheim beliefert den Weltmarkt und steht entsprechend unter Wettbewerbsdruck. Zur Digitalisierung der Fertigung gab es keine Alternative und sie ist noch in der Entwicklung.
Die Firma Zoller beteiligt sich an dem Forschungsprojekt "Smart Tool" der TU Darmstadt. Smart sind diese Tools vor allem, weil sie zum Informationsträger werden.
"Das Werkzeugmanagement ist kein direkt wert schöpfender Prozess. Es ist nur ein Unterstützungsprozess vergleichbar der Logistik in einem Unternehmen und von daher muss man sehen, dass man einerseits die Optimierungspotenziale nutzen kann, andererseits aber den Aufwand in der Fertigung keinesfalls erhöht, denn sonst wird das System nicht akzeptiert von den Mitarbeitern."
Laura Faatz von „Smart Tools" erklärt, dass riesige Datenmengen zu bewältigen sind, um den Werkzeugkreislauf, so wie er besteht, in die Datenwelt zu übertragen und online verfügbar zu machen. Sie arbeitet daran allgemein verbindliche Standards zu entwickeln, um die Einführung der Digitalisierung zu vereinfachen. Investitionen in Smart Tool-Systeme zahlen sich für Firmen nicht unmittelbar aus. Was mit dem Internet der Dinge mit Sicherheit wächst, sind die Datenmengen, ob am Ende auch die gewinne steigen, ist hingegen nicht geklärt. Oliver Holtemöller vom Institut für Wirtschaftsforschung Halle und Professor für Makroökonomik.
Hartmut Hirsch-Kreinsen, Professor für Wirtschafts- und Industriesoziologe an der TU Dortmund, wurde in den wissenschaftlichen Beirat der Plattform Industrie 4.0 berufen, einem Zusammenschluss von Industrieverbänden der Elektrotechnik, des Maschinenbaus, der Informationswirtschaft und Telekommunikation. Er befasst sich mit Fragen der Zukunft der Arbeitswelt.
"In der Innovationsforschung kann man das als "disruptive innovation" bezeichnen. Konsequenzen, die jetzt nicht hundertprozentig übersehbar sind, die aber deutliche Strukturveränderungen - im Hinblick auf Technik, auf Organisation, aber auch im Hinblick auf Personal, nach sich ziehen. Und das hat zur Konsequenz, dass die disruptiven Innovationen auch ihre eigenen Widersprüche mittransportieren. Es ist teuer. Der Aufwand ist immens. Allein die Datenbestände anzugleichen, Datenbestände zu portieren! Das ist kein Prozess, den man von heute auf morgen lösen kann."
Im Industriegebiet von Pleidelsheim, auf der grünen Wiese und gleichzeitig strategisch an der A81 im Einzugsbereich der Automobilindustrie im Raum Stuttgart gelegen, montiert das mittelständische Unternehmen Zoller Messgeräte für den Maschinenbau, auch "zerspanende Industrie" genannt. Nach außen: Kein High-Tech-Image, sondern schwäbische Gediegenheit.
Als mittelständisches Unternehmen hat Zoller den aufwendigen Schritt in die Digitalisierung seiner Fertigung vollzogen.
Jedes einzelne Teil, das Michael Staib in das Gehäuse vor ihm einsetzt, hat eine IP Adresse. Entweder wurde es so schon angeliefert oder erhält im Werk eine Kennung. Ob ein bestimmtes Werkstück im Lager oder schon verbaut ist, das ist jederzeit und überall online abrufbar. Nachdem die Unternehmensorganisation und -planung mit ERP Systemen, Enterprise Planning Systems, durchdrungen wurde, folgt jetzt die Produktionswelt, das Internet der Dinge. Michael Staib, die Haare hinten zum Pferdeschwanz gebunden, die Arme tätowiert, ist von Beruf eigentlich Kraftfahrzeugmechaniker. Ein festes Berufsbild für seinen Arbeitsplatz gibt es noch nicht.
"Hierfür braucht es schon ein ordentliches Brain. Sie haben hier alles: Sie haben Elektrik, Sie haben Pneumatik, Sie haben Software, Sie haben Ultragenauigkeit und Sie müssen handwerklich unglaublich geschickt sein. Wir schreiben immer 3 Stellen hinter Null. D.h. ich setze dieses Gerät mechanisch im Tausendstelbereich zusammen. Und dann gehe ich mit der Software noch mal drüber, damit der Kunde wirklich im optimalen My-Bereich messen kann."
Wenn er alle Teile verbaut hat, überprüft er alles am Bildschirm. Erst nach einem virtuellen Probelauf, folgt der reale Testlauf. Die Digitalisierung der Arbeitsabläufe war für den Messgerätehersteller Zoller ein notwendiger Schritt, um konkurrenzfähig zu bleiben, erklärt Vertriebsleiter Bernd Schwennig.
"Es ist wichtig, dass insbesondere die zerspanende Industrie, die arbeitsintensiv ist, so gestaltet wird, dass diese Arbeitsplätze auch in Deutschland erhalten bleiben und der Mittelstand zusammenarbeitet, gemeinsam versucht vorhandene Verbesserungspotentiale so zu optimieren, damit auch in 10, 20 Jahren der Fertigungsstandort Deutschland noch attraktiv ist. Wir sind in der Lage mit der ganzen Welt zu konkurrieren und in Deutschland teilweise kostengünstig zu produzieren als in China."
Messgeräte für den Transport nach Übersee, in die USA, und eben auch China, stehen, in großen Holzkisten verpackt, bereit. Das Unternehmen aus Pleidelsheim beliefert den Weltmarkt und steht entsprechend unter Wettbewerbsdruck. Zur Digitalisierung der Fertigung gab es keine Alternative und sie ist noch in der Entwicklung.
Die Firma Zoller beteiligt sich an dem Forschungsprojekt "Smart Tool" der TU Darmstadt. Smart sind diese Tools vor allem, weil sie zum Informationsträger werden.
"Das Werkzeugmanagement ist kein direkt wert schöpfender Prozess. Es ist nur ein Unterstützungsprozess vergleichbar der Logistik in einem Unternehmen und von daher muss man sehen, dass man einerseits die Optimierungspotenziale nutzen kann, andererseits aber den Aufwand in der Fertigung keinesfalls erhöht, denn sonst wird das System nicht akzeptiert von den Mitarbeitern."
Laura Faatz von „Smart Tools" erklärt, dass riesige Datenmengen zu bewältigen sind, um den Werkzeugkreislauf, so wie er besteht, in die Datenwelt zu übertragen und online verfügbar zu machen. Sie arbeitet daran allgemein verbindliche Standards zu entwickeln, um die Einführung der Digitalisierung zu vereinfachen. Investitionen in Smart Tool-Systeme zahlen sich für Firmen nicht unmittelbar aus. Was mit dem Internet der Dinge mit Sicherheit wächst, sind die Datenmengen, ob am Ende auch die gewinne steigen, ist hingegen nicht geklärt. Oliver Holtemöller vom Institut für Wirtschaftsforschung Halle und Professor für Makroökonomik.
Wirtschaftlicher Erfolg durch Digitalisierung nach nicht bei allen
"Wir haben einen langfristigen Trend in Deutschland einer Zunahme der Produktivität von einem Prozent pro Jahr. Das ist der langfristige Durchschnitt und ich erwarte nicht, dass von der Digitalisierung, von Industrie 4.0 ein Produktivitätssprung ausgeht, sondern das wird sich einbetten in diesen stetigen Prozess der Verbesserung der Arbeitsprozesse."
Mit Blick auf die Zahlen der Leistungsbilanz erklärt Oliver Holtemöller, das Kapital sehe derzeit bessere Anlagemöglichkeiten im Ausland. Geld fließt auch in Spekulationsgeschäfte an den Börsen. Industrie 4.0 hat das allgemeine Investitionsklima nicht wesentlich verbessert, obwohl der Begriff gerade das erzeugen sollte: Aufbruchsstimmung in ein neues technisches Zeitalter, Versprechen auf Gewinn. Der wirtschaftliche Erfolg durch Digitalisierung und Vernetzung scheint bisher auf einzelne Unternehmen begrenzt zu sein.
"Wir nehmen viele kleine Teile und bündeln sie zu einem größeren Teil, der dann am Markt bestehen kann. Die Crowd, die Menge an Einzelteilen ist die Basis für unser Geschäft und durch die Vernetzung schaffen wir eine größere Einheit daraus."
Bei den einzelnen Teilen handelt es sich um Biogasanlagen, Blockheizkraftwerke und Photovoltaikanlagen. Deren Energieleistung bündelt NextKraftwerke und schafft damit eine größere Einheit, ein virtuelles Kraftwerk. Auf diese Weise hat das junge Unternehmen im Jahr 2013 zwei Terrawattstunden an den Strommarkt gebracht, erklärt Jan Aengenvoort von Nextkraftwerke.
"Das entspricht ungefähr dem Stromverbrauch einer mittelgroßen Stadt oder aller privater Haushalte einer Großstadt."
An der Idee, die Leistung dezentraler kleiner Energieerzeuger zu bündeln und damit ein „virtuelles Großkraftwerk" zu schaffen, hatten bereits verschiedene Forschungsinstitute gearbeitet und sie tun es immer noch. Trotzdem haben Hendrik Sämisch und Jochen Schwill 2009 in Köln das virtuelle Kraftwerk NextKraftwerke gegründet. Sie fanden genügend Betreiber, die bereit waren, mit ihnen gemeinsam den Beweis anzutreten, dass viele kleine Energieerzeuger von erneuerbarer Energie nicht nur in der Lage sind Strom zu liefern, sondern auch Verantwortung für die Netzstabilität übernehmen können. Dies leisten zu können hatten, so Jan Aengenvoort, die großen Energiebetreiber bis dahin allein für sich beansprucht.
"Das ist natürlich Überzeugungsarbeit gewesen und wir sind sehr glücklich, dass wir das mit vielen hundert Betreibern in ganz Deutschland in kurzer Zeit bewerkstelligen konnten."
Schließlich müssen die Betreiber es zulassen, dass NextKraftwerke über die NextBox Zugriff auf ihre Anlage hat. Aber sie profitieren auch davon, denn mit einer durchschnittlichen Leistung von 400 Kilowatt bis 2 Megawatt kann ein Betrieb allein nicht als Anbieter auf dem Strommarkt auftreten.
In der Vertriebsabteilung liegt eine NextBox zu Vorführzwecken bereit. Ein kompaktes Gerät, das man in Anbetracht von Größe und Gewicht locker unter den Arm nehmen kann. Das Innere besteht im Wesentlichen aus einem Modem und der Steuerungseinheit, die NextKraftwerke selbst entwickelt hat.
"Die Ansteuerung selbst funktioniert über das Handynetz und dann gibt es ein Signal, das wir über diese Box an die Anlage senden können, worauf die Anlage reagiert und seine Stromproduktion anpasst."
Es ist eine komplexe Wirklichkeit, die die Ingenieure von NextKraftwerke erfassen und in den Algorithmus der Steuerung umsetzen müssen. Denn angenommen, durch ein schweres Gewitter fallen Photovoltaik-Anlagen in einer Region aus, dann müssen Anlagen einer anderen Region automatisch hochgefahren werden. Und das ist nur ein Faktor von vielen anderen, der in die „Parametrisierung" einfließen muss. Zudem müssen immer auch die Interessen der Erzeuger berücksichtigt werden.
"Ganz wichtig ist für uns, dass wir ein sehr zuverlässiges und schnelles Telekommunikationsnetz haben, um die 1500 Anlagen, die wir inzwischen vernetzt haben, steuern zu können. Dafür brauchen wir ein sehr stabiles Handynetz und schnelles Internet. Das war vor zehn Jahren noch nicht abzusehen, dass das in dieser Breite, in der wir es heute haben, so gut funktioniert. Das ist für uns sehr sehr wichtig. Und zum anderen gab es in den Rahmenbedingungen eine entscheidende Änderung. Das ist mit EEG 2012 passiert. Bis Anfang 2012 durften erneuerbare Energien nicht ohne weiteres an dem Markt teilnehmen."
Die Novellierung des EEG, das Erneuerbare-Energien-Gesetzes, das am ersten Januar 2012 in Kraft trat, hat feste Einspeisevergütungen für erneuerbare Energien festgelegt. Mit günstigen Rahmenbedingungen und eigenen technischen Innovationen ist aus dem Startup in fünf Jahren ein Unternehmen mit 70 Mitarbeitern geworden.
Mit Blick auf die Zahlen der Leistungsbilanz erklärt Oliver Holtemöller, das Kapital sehe derzeit bessere Anlagemöglichkeiten im Ausland. Geld fließt auch in Spekulationsgeschäfte an den Börsen. Industrie 4.0 hat das allgemeine Investitionsklima nicht wesentlich verbessert, obwohl der Begriff gerade das erzeugen sollte: Aufbruchsstimmung in ein neues technisches Zeitalter, Versprechen auf Gewinn. Der wirtschaftliche Erfolg durch Digitalisierung und Vernetzung scheint bisher auf einzelne Unternehmen begrenzt zu sein.
"Wir nehmen viele kleine Teile und bündeln sie zu einem größeren Teil, der dann am Markt bestehen kann. Die Crowd, die Menge an Einzelteilen ist die Basis für unser Geschäft und durch die Vernetzung schaffen wir eine größere Einheit daraus."
Bei den einzelnen Teilen handelt es sich um Biogasanlagen, Blockheizkraftwerke und Photovoltaikanlagen. Deren Energieleistung bündelt NextKraftwerke und schafft damit eine größere Einheit, ein virtuelles Kraftwerk. Auf diese Weise hat das junge Unternehmen im Jahr 2013 zwei Terrawattstunden an den Strommarkt gebracht, erklärt Jan Aengenvoort von Nextkraftwerke.
"Das entspricht ungefähr dem Stromverbrauch einer mittelgroßen Stadt oder aller privater Haushalte einer Großstadt."
An der Idee, die Leistung dezentraler kleiner Energieerzeuger zu bündeln und damit ein „virtuelles Großkraftwerk" zu schaffen, hatten bereits verschiedene Forschungsinstitute gearbeitet und sie tun es immer noch. Trotzdem haben Hendrik Sämisch und Jochen Schwill 2009 in Köln das virtuelle Kraftwerk NextKraftwerke gegründet. Sie fanden genügend Betreiber, die bereit waren, mit ihnen gemeinsam den Beweis anzutreten, dass viele kleine Energieerzeuger von erneuerbarer Energie nicht nur in der Lage sind Strom zu liefern, sondern auch Verantwortung für die Netzstabilität übernehmen können. Dies leisten zu können hatten, so Jan Aengenvoort, die großen Energiebetreiber bis dahin allein für sich beansprucht.
"Das ist natürlich Überzeugungsarbeit gewesen und wir sind sehr glücklich, dass wir das mit vielen hundert Betreibern in ganz Deutschland in kurzer Zeit bewerkstelligen konnten."
Schließlich müssen die Betreiber es zulassen, dass NextKraftwerke über die NextBox Zugriff auf ihre Anlage hat. Aber sie profitieren auch davon, denn mit einer durchschnittlichen Leistung von 400 Kilowatt bis 2 Megawatt kann ein Betrieb allein nicht als Anbieter auf dem Strommarkt auftreten.
In der Vertriebsabteilung liegt eine NextBox zu Vorführzwecken bereit. Ein kompaktes Gerät, das man in Anbetracht von Größe und Gewicht locker unter den Arm nehmen kann. Das Innere besteht im Wesentlichen aus einem Modem und der Steuerungseinheit, die NextKraftwerke selbst entwickelt hat.
"Die Ansteuerung selbst funktioniert über das Handynetz und dann gibt es ein Signal, das wir über diese Box an die Anlage senden können, worauf die Anlage reagiert und seine Stromproduktion anpasst."
Es ist eine komplexe Wirklichkeit, die die Ingenieure von NextKraftwerke erfassen und in den Algorithmus der Steuerung umsetzen müssen. Denn angenommen, durch ein schweres Gewitter fallen Photovoltaik-Anlagen in einer Region aus, dann müssen Anlagen einer anderen Region automatisch hochgefahren werden. Und das ist nur ein Faktor von vielen anderen, der in die „Parametrisierung" einfließen muss. Zudem müssen immer auch die Interessen der Erzeuger berücksichtigt werden.
"Ganz wichtig ist für uns, dass wir ein sehr zuverlässiges und schnelles Telekommunikationsnetz haben, um die 1500 Anlagen, die wir inzwischen vernetzt haben, steuern zu können. Dafür brauchen wir ein sehr stabiles Handynetz und schnelles Internet. Das war vor zehn Jahren noch nicht abzusehen, dass das in dieser Breite, in der wir es heute haben, so gut funktioniert. Das ist für uns sehr sehr wichtig. Und zum anderen gab es in den Rahmenbedingungen eine entscheidende Änderung. Das ist mit EEG 2012 passiert. Bis Anfang 2012 durften erneuerbare Energien nicht ohne weiteres an dem Markt teilnehmen."
Die Novellierung des EEG, das Erneuerbare-Energien-Gesetzes, das am ersten Januar 2012 in Kraft trat, hat feste Einspeisevergütungen für erneuerbare Energien festgelegt. Mit günstigen Rahmenbedingungen und eigenen technischen Innovationen ist aus dem Startup in fünf Jahren ein Unternehmen mit 70 Mitarbeitern geworden.
Verbesserungen im Ausbau des Breitbandnetzes und bei der Internetsicherheit sind zum Beispiel für das mittelständische Unternehmen FORCAM wichtig. In Friedrichshafen, im Süden der Republik, mit unverstelltem Blick auf den Bodensee, hat Franz Eduard Gruber vor gut zehn Jahren das Unternehmen gegründet. FORCAM steht für "For Computer Aided Manufacturing". Mit der betriebseigenen Technik und Software erfasst FORCAM Daten in Echtzeit von Maschinen oder Fertigungsanlagen großer Automobilhersteller.
"Die deutschen Unternehmen haben erkannt, dass sie den Einsatz ihrer teuren Produktionsmittel auch messen müssen. Sie müssen dafür sorgen, dass die Maschinen und Anlagen an ihr Optimum herangeführt werden. Und das bedeutet Daten zu erfassen in Echtzeit, damit wir Verschwendung feststellen können. Damit wir diese Lean-Philosophie durchsetzen können. What you can not measure, you can not improve. Was man nicht messen kann, das kann man nicht verbessern und deshalb haben die deutschen Automobilisten angefangen neue Technik einzuführen, die Digitalisierung der Produktion, um ihre Maschinen und Anlagen datentechnisch zu erfassen, um die Leistung zu messen und um mit geeigneten Maßnahmen die Produktivität zu steigern."
Entwicklungsstränge werden zusammengeführt
Für Franz Eduard Gruber und seinen Partner Alexander Schließmann ist dies die logische Zusammenführung zweier Entwicklungsstränge in der Industrie: der Automatisierung und der Computerisierung. In den 1990er Jahren war die Automatisierung zum Stillstand gekommen, weil es zu aufwendig und unwirtschaftlich war, Maschinen miteinander zu vernetzen. Das ist jetzt technisch ohne weiteres möglich und verändert den Zugriff des Menschen auf die Maschine, erklärt der Informatiker Alexander Schließmann.
"Ziel von Industrie 4.0 ist: Eine Maschine liefert Daten. Mit der entsprechenden Logik wird daraus Information. Information, die dem Menschen so aufbereitet wird, dass er die Entscheidungen treffen kann, in welche Richtung er optimiert. Wir werden in Zukunft Verbesserungen sehen, dass die Entscheidungen nicht ausschließlich beim Menschen liegt, sondern eben auch bei der Maschine. Dann kann der Mensch unterstützt werden bei der Entscheidungsfindung, in dem die Maschine intelligenter wird, die entsprechenden Algorithmen hat. Aus der Vergangenheit lernen in Richtung wie sie sich selber optimiert. Aber auch hier: Der Mensch ist die letzte Instanz."
Doch wie definiert sich der Mensch in der Kommunikation mit Maschinen und demnächst auch mit Robotern, die mit immer menschen-ähnlicheren Fähigkeiten ausgestattet werden? Welches Eigenleben oder Regime die Roboter, Maschinen und Produkte führen werden, erfasst allein die Science-Fiction-Phantasie. Noch vor wenigen Jahren war undenkbar, dass ein Auto selbstständig bremst, wenn ein Fußgänger die Straße kreuzt. Das sich selbststeuernde Automobil ist bereits in der Testphase
Auf der diesjährigen Automatica, der Robotermesse in München, präsentieren Hersteller eine neue Generation von leistungsstarken Robotern. Sie agieren nicht mehr im Glasgehäuse, sondern bewegen sich frei im Raum. Sie werden als Assistenten bezeichnet, d.h. sie sollen künftig dem Menschen assistieren – im Servicebereich und der Industrie. Ausgestattet mit Sensoren, online steuerbar über ein Tablet, gelten sie als ausgesprochen feinfühlig.
Doch wie definiert sich der Mensch in der Kommunikation mit Maschinen und demnächst auch mit Robotern, die mit immer menschen-ähnlicheren Fähigkeiten ausgestattet werden? Welches Eigenleben oder Regime die Roboter, Maschinen und Produkte führen werden, erfasst allein die Science-Fiction-Phantasie. Noch vor wenigen Jahren war undenkbar, dass ein Auto selbstständig bremst, wenn ein Fußgänger die Straße kreuzt. Das sich selbststeuernde Automobil ist bereits in der Testphase
Auf der diesjährigen Automatica, der Robotermesse in München, präsentieren Hersteller eine neue Generation von leistungsstarken Robotern. Sie agieren nicht mehr im Glasgehäuse, sondern bewegen sich frei im Raum. Sie werden als Assistenten bezeichnet, d.h. sie sollen künftig dem Menschen assistieren – im Servicebereich und der Industrie. Ausgestattet mit Sensoren, online steuerbar über ein Tablet, gelten sie als ausgesprochen feinfühlig.
".....unsere Simulationsumgebung ist für jeden Funktionszusammenhang aus dem Industrie 4.0 Instrumentarium und beantwortet Fragen....."
Der Care-O-Bot 3, ein silberfarbenes Etwas auf vier Rädern, einssechzig gross - zeigt, dass er sich auf einer zimmer-großen Fläche ohne weiteres zurecht finden kann, gezielt einen Papierkorb ansteuern und ihn exakt in den dafür vorgesehenen Behälter leeren kann. Das Fraunhofer-Institut für Produktionstechnik und Automatisierung in Stuttgart hat den Care-O-Bot mit finanzieller Beteiligung der Dussmann GmbH entwickelt. Dussmann, spezialisiert auf Gebäudereinigung, mit einem Umsatz von fast 2 Milliarden Euro im Jahr, ist Projektpartner. Als Informatiker ist Joshua Hampp an dem Forschungsprojekt beteiligt.
"Hier ist der Care-O-Bot 3, eine Forschungsplattform, die wir benutzen, um neue Technologien zu entwickeln. Das besondere ist, dass er eine mobile Plattform hat. Zusätzlich ist ein Arm verbaut, ein Manipulator, mit dem man Gegenstände fassen kann, bewegen kann. Es ist ein 3D Kamerasystem verbaut, mit dem er die Umgebung dreidimensional erfasst, um Kollisionen zu vermeiden."
In Zukunft soll der Service-Roboter alle Haushaltstätigkeiten eigenständig verrichten können: Heben, wahrnehmen, analysieren, erkennen, interpretieren, reagieren. Der Haushalt, angefangen vom selbsttätigen Türen öffnen, dem Trinken und Essen reichen, ist die Blaupause für die universellen Fähigkeiten des Roboters, erklärt Joshua Hampp.
Der Care-O-Bot 3, ein silberfarbenes Etwas auf vier Rädern, einssechzig gross - zeigt, dass er sich auf einer zimmer-großen Fläche ohne weiteres zurecht finden kann, gezielt einen Papierkorb ansteuern und ihn exakt in den dafür vorgesehenen Behälter leeren kann. Das Fraunhofer-Institut für Produktionstechnik und Automatisierung in Stuttgart hat den Care-O-Bot mit finanzieller Beteiligung der Dussmann GmbH entwickelt. Dussmann, spezialisiert auf Gebäudereinigung, mit einem Umsatz von fast 2 Milliarden Euro im Jahr, ist Projektpartner. Als Informatiker ist Joshua Hampp an dem Forschungsprojekt beteiligt.
"Hier ist der Care-O-Bot 3, eine Forschungsplattform, die wir benutzen, um neue Technologien zu entwickeln. Das besondere ist, dass er eine mobile Plattform hat. Zusätzlich ist ein Arm verbaut, ein Manipulator, mit dem man Gegenstände fassen kann, bewegen kann. Es ist ein 3D Kamerasystem verbaut, mit dem er die Umgebung dreidimensional erfasst, um Kollisionen zu vermeiden."
In Zukunft soll der Service-Roboter alle Haushaltstätigkeiten eigenständig verrichten können: Heben, wahrnehmen, analysieren, erkennen, interpretieren, reagieren. Der Haushalt, angefangen vom selbsttätigen Türen öffnen, dem Trinken und Essen reichen, ist die Blaupause für die universellen Fähigkeiten des Roboters, erklärt Joshua Hampp.
Neue Entwicklung wird vor allem Fragen aufwerfen
"Unser Roboter interagiert aber auch mit anderen Robotern, d.h. mit anderen Werkzeugmaschinen, die vorhanden sind und kann fließend integriert werden, kann sich bekannt machen. Er kann seine Fähigkeiten äußern, dass er einen Manipulator hat und damit z.B. Werkstücke transportieren könnte - per WLAN, per Funk."
Auf dem Karriereforum IKOM an der TU München erklärt Siemens Vorstand Klaus Helmrich Studenten, worauf es in der neuen Welt von Industrie 4.0 ankommt.
"Das ist der Ansatz von Industrie 4.0. Produktion, Design, Service in einer durchgängigen Kette zu steuern. Nur so wird man effiziente Prozesse erreichen."
Studenten organisieren diese Messe, um Unternehmen und angehende Ingenieure miteinander bekannt zu machen. Ausgesprochen konventionell treten sie auf: Im schwarzen Anzug mit grell grüner Krawatte, verstehen sich als Dienstleister für die Wirtschaft und setzen bewährte Routinen einfach fort. Ein innovativeres Umfeld stellt sich Siemens-Vorstand Klaus Helmrich vor. Das lässt er durchblicken, wenn er über seine Besuche im amerikanischen Silicon Valley spricht und die Kreativität, auf die er dort stößt. Aber auch Siemens-Vorstand Helmrich vermag keine Aufbruchsstimmung zu verbreiten. Die Siemens-Werksphilosophie wird einen kreativen Freigeist vermutlich nicht stimulieren.
Auf dem Karriereforum IKOM an der TU München erklärt Siemens Vorstand Klaus Helmrich Studenten, worauf es in der neuen Welt von Industrie 4.0 ankommt.
"Das ist der Ansatz von Industrie 4.0. Produktion, Design, Service in einer durchgängigen Kette zu steuern. Nur so wird man effiziente Prozesse erreichen."
Studenten organisieren diese Messe, um Unternehmen und angehende Ingenieure miteinander bekannt zu machen. Ausgesprochen konventionell treten sie auf: Im schwarzen Anzug mit grell grüner Krawatte, verstehen sich als Dienstleister für die Wirtschaft und setzen bewährte Routinen einfach fort. Ein innovativeres Umfeld stellt sich Siemens-Vorstand Klaus Helmrich vor. Das lässt er durchblicken, wenn er über seine Besuche im amerikanischen Silicon Valley spricht und die Kreativität, auf die er dort stößt. Aber auch Siemens-Vorstand Helmrich vermag keine Aufbruchsstimmung zu verbreiten. Die Siemens-Werksphilosophie wird einen kreativen Freigeist vermutlich nicht stimulieren.
"Da gibt es eine Einstellung, die heißt wie folgt, das geht durch die ganze Belegschaft: Heute sind wir gut und morgen sind wir besser. Und morgen sagen wir exakt das gleiche. Und das ist eine tolle Umgebung, wenn man da mitspielen darf, mit dabei sein darf. Danke schön."
Anschließend wollen Studenten vom Siemens-Vorstand nicht wissen, wie er sich die Ausbildung zum Datenwissenschaftler, dem Data Scientist vorstellt, der künftig die wachsenden Datenströme analysieren und einordnen soll, sondern warum Siemens Arbeitsplätze abbaut. Johannes Röder studiert an der TU München Maschinenbau.
"Was ist mit dem Rest der Gesellschaft, der dieses Fachwissen nicht hat? In dieser Welt finden die keine Arbeit mehr! In der Industrie 4.0.! Und dann ist die Frage wie Unternehmen wie Siemens Verantwortung tragen. Gesellschaftlich. Für die gesamte Gesellschaft. Oder ob der Staat das regeln muss?"
Den zukünftigen Ingenieur hat ein Seminar zu Soft Skills – zu sozialer Kompetenz - nachdenklich gemacht.
"Ich besuche dieses Semester einen Soft Skill Kurs. Wir als Maschinenbauer müssen Soft Skills belegen, weil wir sozial inkompetent sind und da gibt es einen Kurs, der sich mit Technikphilosophie befasst, den ich extrem gut finde. Denn dort erfährt man eine andere Denkweise. Dass man die ganze Sache im Kontext sieht und nicht nur: Was muss ich machen, um eine neue Technologie zu entwickeln? Ohne zu fragen, was sind die gesellschaftlichen Konsequenzen!"
Die Digitalisierung und Vernetzung der Produktion wird vor allem Fragen aufwerfen, wie der Datenaustausch, die Datensicherheit, das Recht auf die eigenen Daten geregelt werden und welche Interessen dabei zum Zuge kommen. Probleme von und für Spezialisten. Nach Revolution kling das alles nicht – oder noch nicht. Vielleicht wird sie ja noch geschrieben, die große Erzählung von der Industrie 4.0, die es braucht um Menschen und vor allem Investoren anzuziehen.
"Bei der Internetblase, die wir um die Jahrtausendwende gehabt haben, da war die Geschichte, dass durch die Einführung und Verbreitung des Internets Produktivität sich dauerhaft erhöhen wird, dass wir dauerhaft ein Wirtschaftswachstum hätten. Das hat sehr viele Investitionen finanziert, diese Geschichte. Das hat dazu geführt, dass auch Dinge entwickelt worden sind, die ohne diese Finanzierung, ohne diese Übertreibung niemals finanziert worden wären."
Das Smartphone hat Apple-Gründer Steve Jobs als technische Spielerei auf den Markt gebracht: Der Zugriff auf das mobile Internet mit einem Gerät, das in die Handfläche passt! Innerhalb weniger Jahre hat es den Markt erobert.
Die Zukunftsprojektionen von Industrie 4.0, der Digitalisierung und Vernetzung industrieller Produktionssysteme, reichen bis in das Jahr 2025. Doch die großen industriellen Umwälzungen der Vergangenheit haben gezeigt: Sie sind nicht planbar.
"Was ist mit dem Rest der Gesellschaft, der dieses Fachwissen nicht hat? In dieser Welt finden die keine Arbeit mehr! In der Industrie 4.0.! Und dann ist die Frage wie Unternehmen wie Siemens Verantwortung tragen. Gesellschaftlich. Für die gesamte Gesellschaft. Oder ob der Staat das regeln muss?"
Den zukünftigen Ingenieur hat ein Seminar zu Soft Skills – zu sozialer Kompetenz - nachdenklich gemacht.
"Ich besuche dieses Semester einen Soft Skill Kurs. Wir als Maschinenbauer müssen Soft Skills belegen, weil wir sozial inkompetent sind und da gibt es einen Kurs, der sich mit Technikphilosophie befasst, den ich extrem gut finde. Denn dort erfährt man eine andere Denkweise. Dass man die ganze Sache im Kontext sieht und nicht nur: Was muss ich machen, um eine neue Technologie zu entwickeln? Ohne zu fragen, was sind die gesellschaftlichen Konsequenzen!"
Die Digitalisierung und Vernetzung der Produktion wird vor allem Fragen aufwerfen, wie der Datenaustausch, die Datensicherheit, das Recht auf die eigenen Daten geregelt werden und welche Interessen dabei zum Zuge kommen. Probleme von und für Spezialisten. Nach Revolution kling das alles nicht – oder noch nicht. Vielleicht wird sie ja noch geschrieben, die große Erzählung von der Industrie 4.0, die es braucht um Menschen und vor allem Investoren anzuziehen.
"Bei der Internetblase, die wir um die Jahrtausendwende gehabt haben, da war die Geschichte, dass durch die Einführung und Verbreitung des Internets Produktivität sich dauerhaft erhöhen wird, dass wir dauerhaft ein Wirtschaftswachstum hätten. Das hat sehr viele Investitionen finanziert, diese Geschichte. Das hat dazu geführt, dass auch Dinge entwickelt worden sind, die ohne diese Finanzierung, ohne diese Übertreibung niemals finanziert worden wären."
Das Smartphone hat Apple-Gründer Steve Jobs als technische Spielerei auf den Markt gebracht: Der Zugriff auf das mobile Internet mit einem Gerät, das in die Handfläche passt! Innerhalb weniger Jahre hat es den Markt erobert.
Die Zukunftsprojektionen von Industrie 4.0, der Digitalisierung und Vernetzung industrieller Produktionssysteme, reichen bis in das Jahr 2025. Doch die großen industriellen Umwälzungen der Vergangenheit haben gezeigt: Sie sind nicht planbar.