Industriestandort Deutschland
Aus der Zeit gefallen: die Hochöfen 8 und 9 in Duisburg. © imago images / Jochen Tack
Auf dem Weg zur grünen Stahlproduktion
14:34 Minuten
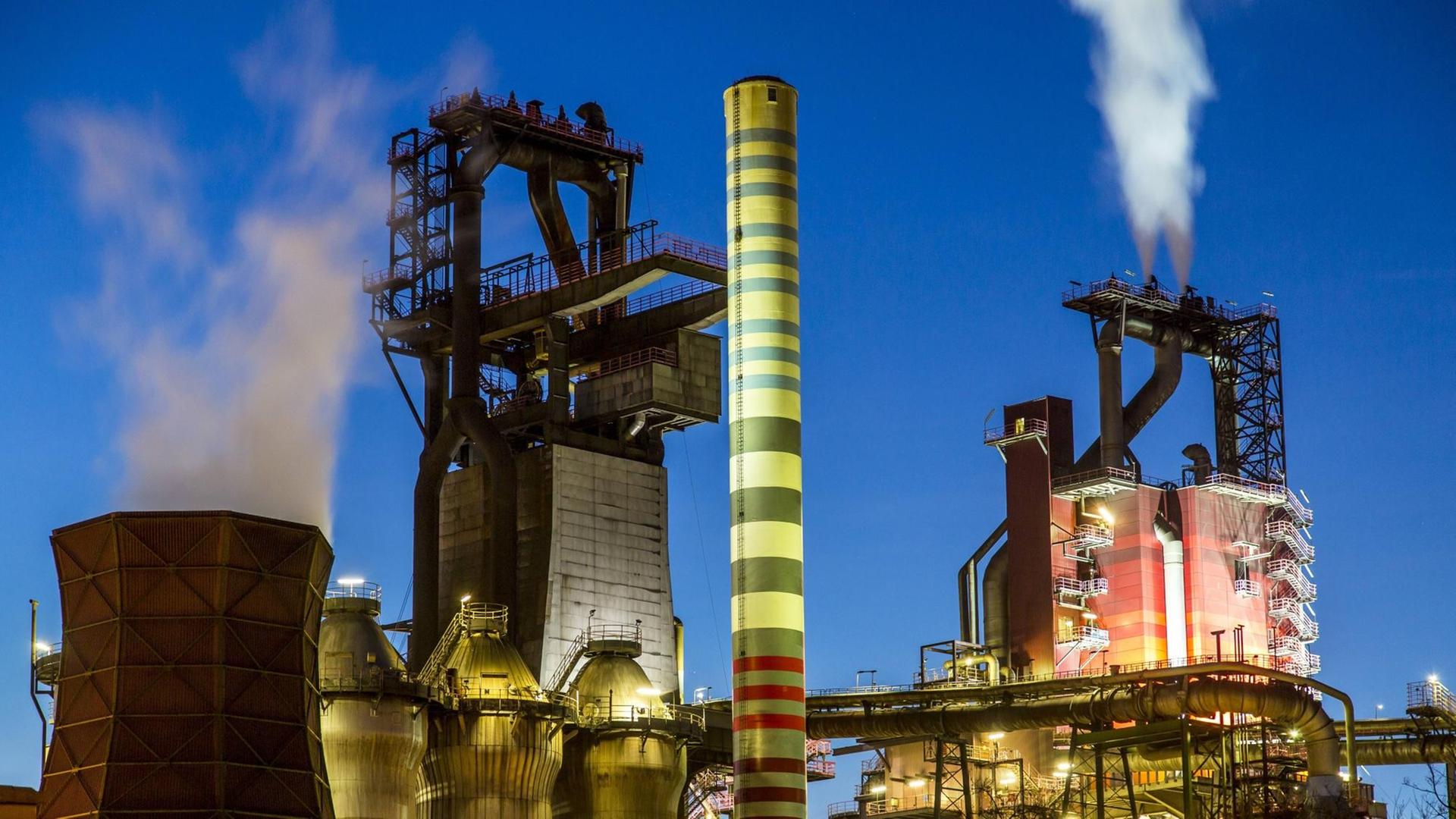
Die Produktion von Stahl braucht jede Menge Energie. Um weniger CO2 zu emittieren, sucht die Industrie derzeit nach Wegen, die klassische Kohle als Energieträger zu ersetzen. Die Branche hofft dabei auch auf die neue Bundesregierung.
Wer die eisernen Stufen zum Hochofen 9 im Stahlwerk von Thyssenkrupp in Duisburg hochklettert und Teile des Werkes überblickt, ahnt, was es bedeutet, in der Stahlindustrie umzusteuern. Am deutlichsten wird das am Hochofen: In der Gießhalle rauscht es, die Feuer flackern, es ist, als habe man eine andere Welt betreten.
Das glühende Roheisen spiegelt sich im schweren, silbernen Schmelzermantel des Stahlarbeiters, während er mit einer Messlatte eine Probe aus dem Roheisen zieht. Per Rohrpost wird diese Probe sogleich ins Labor geschickt, um die Qualität des Eisens zu überprüfen. Noch wird dieses Roheisen produziert wie seit zwei Jahrhunderten. Aber das soll sich in Zukunft ändern, erklärt Roswitha Becker.
Die Ingenieurin leitet das Team "CO2-Forschung und alternative Technologien" bei ThyssenKrupp in Duisburg. Während sie über ihre Arbeit spricht, steht sie etwas abseits auf einer Wiese und blickt auf den Hochofen 9 und die vielen Rohre und Leitungen, die von ihm aus über das Gelände des Werkes führen:
"Der Hochofen ist quasi das Herz der Stahlerzeugung, es ist das Aggregat, bei dem aus Eisenerzen das flüssige Roheisen gewonnen wird. Hier wird dem Eisen der Sauerstoff entzogen. Das machen wir aktuell mit Kohle und Koks und als Produkt entsteht dadurch das flüssige Roheisen, aber eben auch CO2."
50 Jahre alte Technik soll helfen
Und zwar tonnenweise. Deshalb sollen diese Prozesse umgestellt werden, damit auf Dauer eine kohlenfreie und somit CO2-freie Produktion gelingen kann. Einen ersten Zwischenschritt ist man bei ThyssenKrupp auf diesem Weg schon gegangen – ein Hot Briquetted Iron, auch Eisenschwamm genannt, wird eingesetzt. Diesem wurde der Sauerstoff bereits vorher entzogen.
"Bezogen auf die Menge Stahl, also auf den Stahl, der aus diesem Eisen kommt, sind das – selbst wenn man alle indirekten Emissionen berücksichtigt – rund 70 Prozent weniger als bei herkömmlichen Stahl", erklärt Professor Stefan Lechtenböhmer. Er ist der Leiter der Abteilung Zukünftige Energie- und Industriesysteme am Wuppertal Institut und begleitet die technologischen Veränderungen der Stahlproduktion bei ThyssenKrupp.
70 Prozent weniger Emissionen. Das bedeutet konkret, dass das neue Stahlerzeugnis nur noch 600 Kilogramm CO2 verursacht und nicht mehr zwei Tonnen wie bei der herkömmlichen Stahlproduktion. Also eine durchaus sinnvolle Maßnahme, findet Lechtenböhmer.
Die Technologie dahinter ist nicht neu. Sie wurde bereits in der 1970er-Jahren entwickelt und wird in anderen Teilen der Erde, zum Beispiel in Mexiko, bis heute angewandt. Aber in Deutschland war dieses Prozedere schlicht nicht wirtschaftlich. Um den CO2-Ausstoß ganz zu reduzieren, braucht es aber noch wesentlich tiefgreifendere Änderungen in der Stahlproduktion, sagt Lechtenböhmer:
"Die Eisenschwamm-Erzeugung umstellen, erst auf Erdgas, dann grünen Wasserstoff. Und die Weiterverarbeitung des Eisenschwamms in Lichtbogenöfen, oder alternative elektrische Technologien entwickeln."
Strom statt Kohle
In Lichtbogenöfen werden bislang vor allem Stahlschrottprodukte eingeschmolzen, um den Stahl dann wieder zu verwenden. Neuer Stahl entsteht meistens in Hochöfen. ThyssenKrupp plant, bis zum Jahr 2045 CO2-freien Stahl zu produzieren. Ein entscheidender Schritt soll dabei sein, den Eisenschwamm in Zukunft nicht mehr anzukaufen, sondern selbst herzustellen – und zwar mit Hilfe von grünem Wasserstoff.
Sicher ist: Die archaischen Spektakel mit brennenden Feuern in einem Hochofen werden wohl bald der Vergangenheit angehören – wenn die Stahlindustrie in Deutschland überleben will, dann führe an dieser Revolution kein Weg vorbei, so Roswitha Becker.
Auch Georgsmarienhütte ist eng verbunden mit der Stahlproduktion. Mitte des 19. Jahrhunderts entstand dort ein Hüttenwerk. Auch heute wird in der Stadt bei Osnabrück Stahl produziert.
Anders als im Ruhrgebiet jedoch ohne einen Kohle-Hochofen. Glühend verflüssigt der Elektrolichtbogenofen Eisen bei 1450 Grad Celsius. Eine Glaswand trennt Ingenieur Jean-Frédéric Castagnet, Leiter der Technologie und Innovation, jetzt von seinen Kollegen, die hier im Hauptwerk am Ofen stehen.
Seit 1994 arbeitet die Georgsmarienhütte mit diesem Verfahren, das Schrott mithilfe von elektrischem Strom einschmilzt. Für symbolische zwei D-Mark hatte der frühere RWE-Manager Jürgen Großmann das Werk gekauft.
Die lokalen Kohle- und Erzvorkommen waren längst abgeschürft, und da das Werk nicht mit dem Schiff erreichbar ist, schien ein Weiterbetrieb als klassische Hütte wirtschaftlich nicht möglich. Großmann entschied sich für den Umbau, Hochofen und Gasometer ließ er sprengen. Das Werk stieg auf Recycling um.
"Die Stahlherstellung heutzutage im Elektroofen ist circa fünfmal sauberer als mit einer traditionellen Hochofenroute", erklärt Alexander Becker. Er hat in diesem Sommer den Vorstand der Georgsmarienhütte Holding übernommen.
Es gibt nicht genügend grünen Strom
Doch der Ofen im Stahlwerk ist ein Strom-Großverbraucher. Die gesamte Georgsmarienhütte Gruppe verbrauche mehr Strom als die Stadt Osnabrück mit ihren etwa 160.000 Einwohnern, rechnet Becker vor. Um energieintensiv, aber trotzdem klimafreundlich Stahl herzustellen, benötigt das Unternehmen daher grünen Strom:
"Wir können natürlich auch den Anteil erhöhen. Allerdings kostet es natürlich Geld. Es sind pro Tonne Stahl, die wir produzieren, 50 bis 60 Euro Mehrkosten. Dann würden wir komplett grünen Strom bekommen. Es ist schon möglich, ist eine reine Geldfrage. Und da ist natürlich (auch) die Frage, ob die Endkunden am Ende so etwas zahlen möchten."
Derzeit aber sei das für sein Unternehmen und die Stahlindustrie eigentlich eine hypothetische Frage, sagt Manager Alexander Becker. Denn selbst wenn Kunden bereit wären, diesen Preis zu zahlen: Es gebe einfach nicht genügend Strom.
Die Georgsmarienhütte hat sich zum Ziel gesetzt, ihren Stahl bis 2050 vollkommen klimaneutral herzustellen. Notwendig sei dafür aber elektrische Energie, die aus erneuerbaren Energiequellen produziert wird. Alexander Becker setzt seine Hoffnungen auf die neue Bundesregierung.
Die ganze Branche ist in Gefahr
Im Moment dauert es oft Jahre, ein Windrad genehmigen zu lassen und zu bauen. Auch der Ausbau der Trassen, mit denen vor allem Windenergie aus dem Norden in den Süden fließen soll, stocke seit langem, bemängelt auch Ingenieur Jean-Frederic Castagnet.
Beim Rundgang durch die Hütte zeigt Castagnet auch die Gasbrenner, die sich durch noch glühenden Stahlblöcke fräsen. Nicht nur beim Schneiden des Stahls wird in Georgsmarienhütte Gas eingesetzt. Mit Erdgas erwärmen sie hier auch den Stahl für die Weiterverarbeitung.
Um klimaneutral zu arbeiten, muss das Unternehmen in Zukunft auch diesen CO2-Ausstoß einsparen – voraussichtlich mit grünem Wasserstoff. Doch Georgsmarienhütte-Chef Alexander Becker bleibt skeptisch. Denn für die Produktion von grünem Wasserstoff braucht es gigantische Mengen grünen Stroms, mehr als in Deutschland wohl produziert werden kann.
Darum plant die Georgsmarienhütte selbst, in die Stromerzeugung einzusteigen. Denn alle Gebäude und Werksstandorte sind natürlich potenzielle Photovoltaikkraftwerke:
"Das wird vermutlich aber nur drei bis fünf Prozent unseres Strombedarfs decken. Und wir diskutieren jetzt auch noch mit externen Partnern, wo wir denn Windräder an unsere Grenzen an den Werken setzen können. Wir machen uns jetzt selbst auf den Weg."
Sonst, so sorgen sie sich in Georgsmarienhütte, werde die Stahlproduktion eines Tages aus Deutschland verschwinden.