Schöne, neue Arbeitswelt
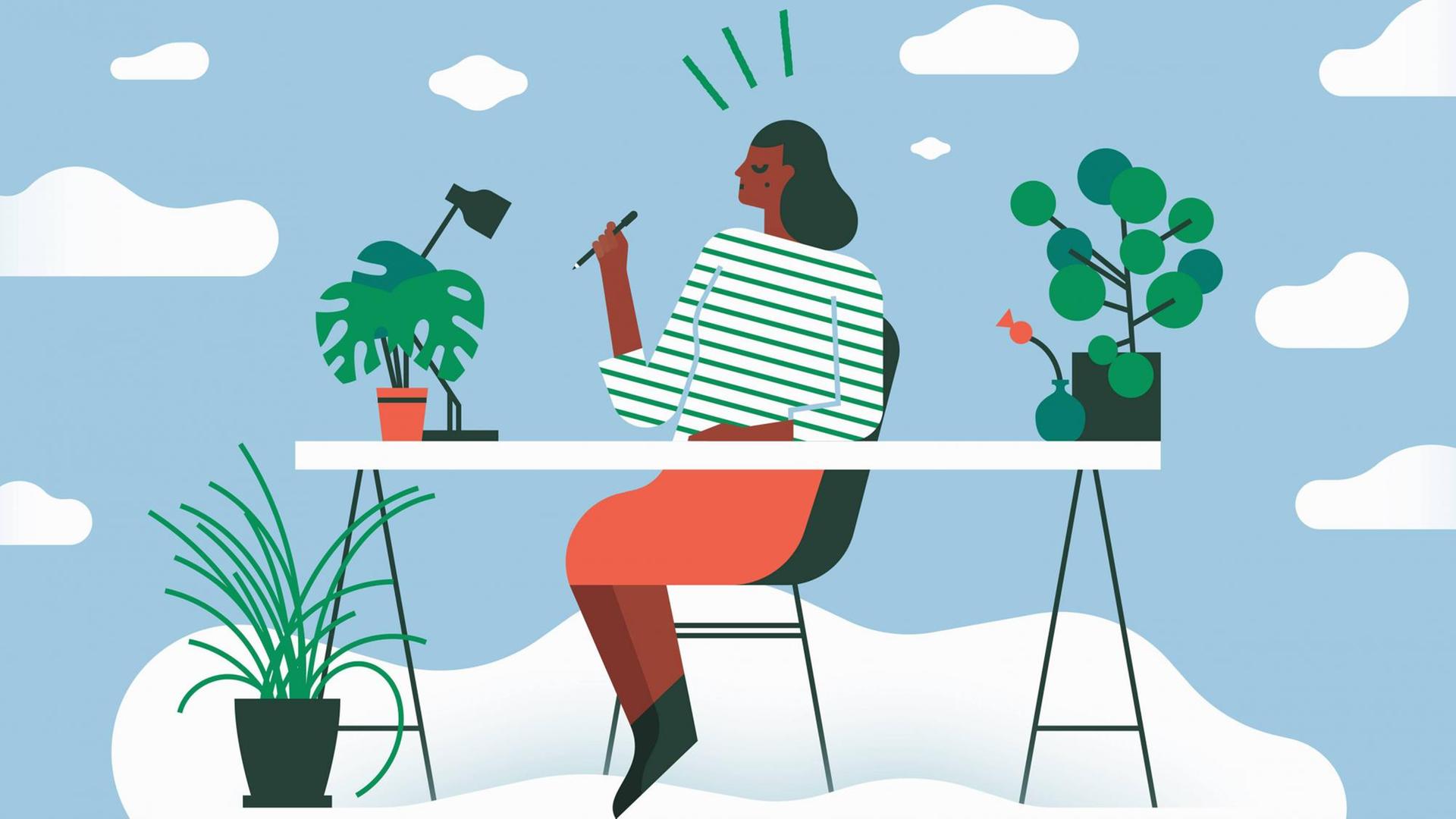
Effektiver, transparenter und selbstbestimmter – mithilfe des Lean-Konzepts soll Büroarbeit "verschlankt" werden. Aber geht es den Firmen wirklich um mehr Effizienz und Mitbestimmung? Oder doch nur darum, aus den Mitarbeitern mehr herauszuholen?
Samstagmorgen. Neun Frauen und Männer sind gekommen. Sachbearbeiterinnen, Freiberufler, Verwaltungsangestellte. Sie sitzen freiwillig an diesem Wochenende in dem Volkshochschulseminar. Sie eint ein Ziel. Sie wollen Zeit sparen. Im Büro. Da kann nämlich viel schiefgehen.
"Ich glaube, dass da viel Zeit auf der Strecke liegenbleibt. Man könnte auf jeden Fall was optimieren, deshalb bin ich hier. … Vor allem was digitale Abspeicherungssystematik angeht. Weil ich auf meinem Rechner immer suchen muss und das nervt mich."
Heike Kobold lächelt mit. Sie ist die Richtige. Eine leidenschaftliche Aufräumerin. Seit zehn Jahren Strategiecoach für Büroorganisation. Sie krempelt die Welt ihrer Kunden um, strukturiert sie neu. Den Arbeitsplatz, eine Abteilung oder gleich das ganze Unternehmen.
Das Zauberwort ihrer Strategie heißt "Lean", übersetzt bedeutet das schmal oder mager. Egal ob im Büro oder in der Produktion, immer geht es darum, Arbeitsprozesse zu verschlanken. Den Workflow schneller, besser, effizienter zu machen. Der Gedanke stammt aus Japan, die Methode nennt sich zu Deutsch 5A. Das erste A steht für Aussortieren.
"Ich glaube, dass da viel Zeit auf der Strecke liegenbleibt. Man könnte auf jeden Fall was optimieren, deshalb bin ich hier. … Vor allem was digitale Abspeicherungssystematik angeht. Weil ich auf meinem Rechner immer suchen muss und das nervt mich."
Heike Kobold lächelt mit. Sie ist die Richtige. Eine leidenschaftliche Aufräumerin. Seit zehn Jahren Strategiecoach für Büroorganisation. Sie krempelt die Welt ihrer Kunden um, strukturiert sie neu. Den Arbeitsplatz, eine Abteilung oder gleich das ganze Unternehmen.
Das Zauberwort ihrer Strategie heißt "Lean", übersetzt bedeutet das schmal oder mager. Egal ob im Büro oder in der Produktion, immer geht es darum, Arbeitsprozesse zu verschlanken. Den Workflow schneller, besser, effizienter zu machen. Der Gedanke stammt aus Japan, die Methode nennt sich zu Deutsch 5A. Das erste A steht für Aussortieren.
Gut strukturiert durch den Tag
"Ich sortiere alles aus, was ich doppelt habe, was ich wirklich nicht mehr brauche. Im zweiten Schritt geht es ums Aufräumen. Wenn ich mich an meinen Schreibtisch setze und so ganz entspannt die Hände bewege, dann nennt man das den kleinen Greifraum. Und in diesen kleinen Greifraum darf alles rein, was ich ganz häufig benutze. Ne Tastatur, die Maus, ein Telefon, ein Kugelschreiber, das darf hier rein. Alles andere hat auf meinem Schreibtisch nix zu suchen."
Klingt ziemlich streng. Amüsierte Blicke. Auf dem Schreibtisch der meisten Teilnehmer sieht´s offenbar anders aus. Heike Kobold kennt diese Reaktion, ist schon beim dritten A: den Arbeitsplatz sauber halten. Und der nächste Schritt: die Anordnung zur Regel machen.
"Auch da gilt, in die oberste Schublade alle Dinge, die ich ganz häufig benutze. Zweite Schublade, Dinge, die ich immer mal wieder benutze. Aber dass ihr auch da überlegt, was nutze ich wirklich?! Der fünfte Schritt ist der böse Schritt: alle Schritte wiederholen."
Klingt ziemlich streng. Amüsierte Blicke. Auf dem Schreibtisch der meisten Teilnehmer sieht´s offenbar anders aus. Heike Kobold kennt diese Reaktion, ist schon beim dritten A: den Arbeitsplatz sauber halten. Und der nächste Schritt: die Anordnung zur Regel machen.
"Auch da gilt, in die oberste Schublade alle Dinge, die ich ganz häufig benutze. Zweite Schublade, Dinge, die ich immer mal wieder benutze. Aber dass ihr auch da überlegt, was nutze ich wirklich?! Der fünfte Schritt ist der böse Schritt: alle Schritte wiederholen."
Wer gut strukturiert sei, könne entspannter arbeiten, sagt Heike Kobold. Die Aufgaben im Büro würden immer umfangreicher, wer keine eigene Struktur für sich finde, gehe unter, glaubt die Strategieexpertin und fügt hinzu.
"Also mein Ziel ist nicht, dass Zeitmanagement so viel Zeit einspart, dass ich noch fünf Aufgaben mehr erledigen kann, sondern dass ich die Aufgaben, die ich habe, entspannter erledigen kann."
Arbeitgeber sehen das oft anders. Lean steht dort eher für Arbeitsverdichtung. Den Grundstein für Lean legte Toyota. Ziel war damals aber nicht, mit weniger Arbeitern mehr Autos zu produzieren, sondern mehr Autos in höherer Qualität. Das Management beteiligte seine Mitarbeiter an diesem Prozess. Sie sollten sich einbringen, auf Defizite hinweisen, selber Lösungen entwickeln. Mit dem Ergebnis, dass die Produktion Schritt für Schritt verbessert wurde. Die Kultur lautete bei Toyota: Je effizienter die Arbeit, desto sicherer der Job. US-amerikanische Unternehmensberater und Wissenschaftler des Bostoner MIT entwickelten das Modell dann weiter und nannten es Lean.
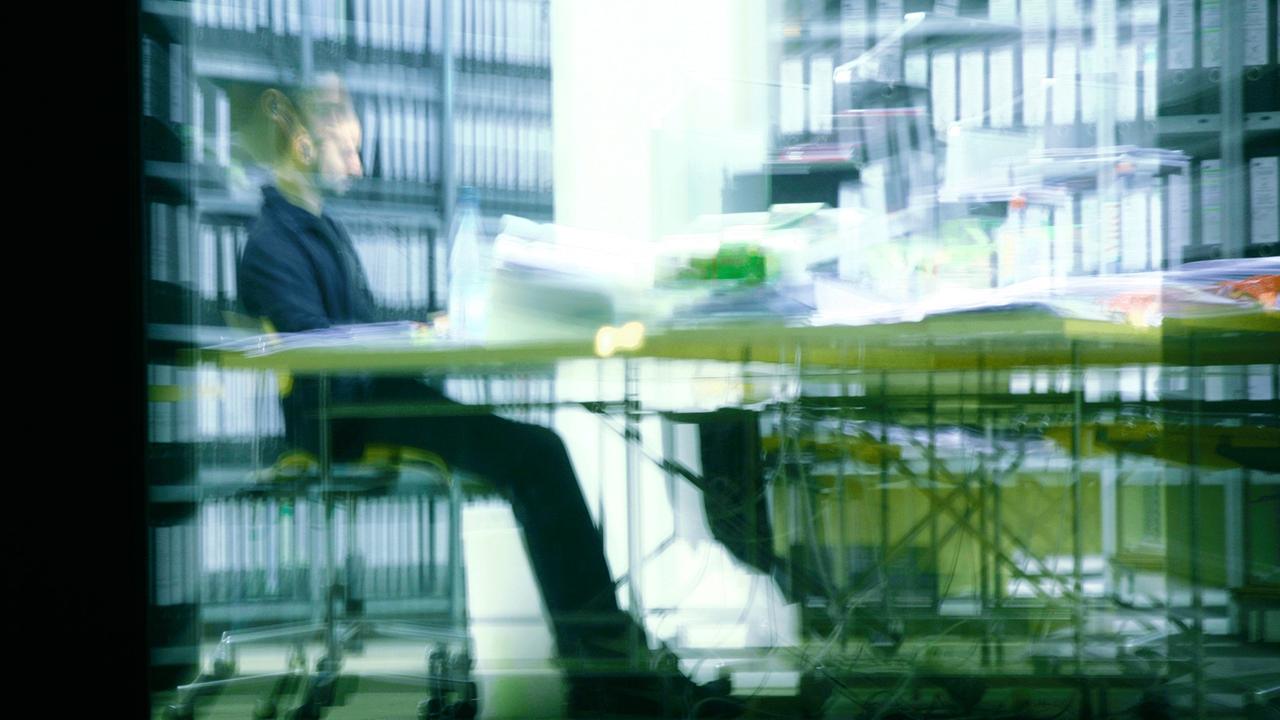
Was bringen schlanke Arbeitsprozesse den Beschäftigten?© picture-alliance / dpa / Wolfram Steinberg
Mitarbeiter sollen stärker einbezogen werden
"Es ist eine Kombination aus unterschiedlichen Prinzipien der Organisation von Produktion. Aber auch der Organisation von Arbeit und des Arbeitseinsatzes. Produktionsprozesse, da ist das Prinzip nur Dinge zu produzieren, die auch unmittelbar gebraucht werden. Also nicht auf Vorrat, auf Lager zu produzieren. Zweites zentrales Element ist, die Arbeitsprozesse möglichst weitgehend zu standardisieren, dass möglichst wenig Fehler passieren, möglichst klare Arbeitsanweisungen auch formuliert werden. Und ein drittes Prinzip, die Beschäftigten in den Prozessen auch stärker einzubeziehen in die Ausgestaltung, in die Optimierung."
Seit mehr als 25 Jahren forscht Martin Kuhlmann am Soziologischen Forschungsinstitut Göttingen zum Thema Lean, das Anfang der 90er nach Deutschland gelangte. Es wird längst nicht mehr nur in der Fertigung angewandt, sondern auch im Büro und in den Entwicklungsabteilungen. Das Fraunhofer-Institut kam in einer Studie zu dem Schluss, dass 30 Prozent aller Bürotätigkeiten Verschwendung seien. Einer Studie des Softwarekonzerns Microsoft zufolge, wenden Beschäftigte etwa 28 Tage im Jahr für Suchen auf. Ob diese Zahlen stimmen? Martin Kuhlmann schüttelt skeptisch den Kopf. Nachgewiesen seien sie jedenfalls nicht, sagt der Arbeitssoziologe. Soll das Modell Erfolg haben, habe die Forschung vor allem eins gezeigt:
"Es ist einfach eine Frage, ob ich die Leute ernst nehme mit ihren Fähigkeiten, mit ihren Qualifikationen. Die müssen nicht hoch ein, die können auf einem mittleren Niveau sein. Und ob ich im Betrieb eine Struktur habe, die in der Lage ist, solche Ideen wirklich aufzunehmen. Da ist ein Aspekt natürlich die Führung. Das muss von oben her gewollt und auch gefördert und auch gelebt werden, wie es in der Managementsprache dann auch heißt. Aber mindestens so wichtig ist, dass die anderen betrieblichen Experten auch diese Impulse aufnehmen."
Dank Lean ist der Bürojob in vielen deutschen Unternehmen jedenfalls nicht mehr das, was er einst war: ein Ort geringer Kontrolle und individueller Gestaltung. Jetzt wird erfasst, wieviel Zeit für eine E-Mail aufgewendet wird, für das Ausfüllen einer Bestellung, für Besprechungen. Manchem Unternehmen kann die Formalisierungssucht nicht weit genug gehen. Dort markiert man mit Farbe auf den Schreibtischen, wo der Bildschirm zu stehen hat, das Telefon oder die Kaffeetasse. Alles schön durchgenormt.
Seit mehr als 25 Jahren forscht Martin Kuhlmann am Soziologischen Forschungsinstitut Göttingen zum Thema Lean, das Anfang der 90er nach Deutschland gelangte. Es wird längst nicht mehr nur in der Fertigung angewandt, sondern auch im Büro und in den Entwicklungsabteilungen. Das Fraunhofer-Institut kam in einer Studie zu dem Schluss, dass 30 Prozent aller Bürotätigkeiten Verschwendung seien. Einer Studie des Softwarekonzerns Microsoft zufolge, wenden Beschäftigte etwa 28 Tage im Jahr für Suchen auf. Ob diese Zahlen stimmen? Martin Kuhlmann schüttelt skeptisch den Kopf. Nachgewiesen seien sie jedenfalls nicht, sagt der Arbeitssoziologe. Soll das Modell Erfolg haben, habe die Forschung vor allem eins gezeigt:
"Es ist einfach eine Frage, ob ich die Leute ernst nehme mit ihren Fähigkeiten, mit ihren Qualifikationen. Die müssen nicht hoch ein, die können auf einem mittleren Niveau sein. Und ob ich im Betrieb eine Struktur habe, die in der Lage ist, solche Ideen wirklich aufzunehmen. Da ist ein Aspekt natürlich die Führung. Das muss von oben her gewollt und auch gefördert und auch gelebt werden, wie es in der Managementsprache dann auch heißt. Aber mindestens so wichtig ist, dass die anderen betrieblichen Experten auch diese Impulse aufnehmen."
Dank Lean ist der Bürojob in vielen deutschen Unternehmen jedenfalls nicht mehr das, was er einst war: ein Ort geringer Kontrolle und individueller Gestaltung. Jetzt wird erfasst, wieviel Zeit für eine E-Mail aufgewendet wird, für das Ausfüllen einer Bestellung, für Besprechungen. Manchem Unternehmen kann die Formalisierungssucht nicht weit genug gehen. Dort markiert man mit Farbe auf den Schreibtischen, wo der Bildschirm zu stehen hat, das Telefon oder die Kaffeetasse. Alles schön durchgenormt.
Formalisierung contra Flexibilität
"Lean hat in vielen Bereichen immer die Gefahr, dass es überzogen wird. Wenn nämlich solche Standard- und Formalisierungsprozesse dazu führen, dass Sachverhalte, die man nicht formalisieren sollte, weil Flexibilität notwendig ist, weil Innovationsfähigkeit notwendig ist, weil auch situatives Reagieren notwendig ist. Also für Bereiche für die das gilt, ist Lean eher schädlich."
Zum Beispiel für die Bereiche Entwicklung und Forschung. Längere Denkprozesse lässt das Modell kaum zu. Die Arbeit mit Lean werde stattdessen immer atemloser, berichten viele Mitarbeiter. So sieht es auch ein Betriebsrat, der unerkannt bleiben möchte. Das Thema ist selbst ihm zu heikel. Nur so viel: Der Mann arbeitet für ein Unternehmen aus dem Maschinen- und Anlagenbau im Süden Deutschlands.
"In unserem Unternehmen fing man mit Lean in der Produktion an und das war anfangs schon etwas kurios. Man fing in den Werkstätten damit an, erst einmal aufzuräumen. Man hat Linien auf den Boden gemalt. Das alles erinnerte uns erst einmal an ‚Schöner Wohnen‘. Doch durch das Aufräumen, dass die Werkzeuge immer am gleichen Platz sind, kam dann doch relativ schnell die Erkenntnis, in Lean steckt auch Sinn. Es hilft, produktiver zu werden und nicht so viel Zeit fürs Suchen zu verschwenden."
Nicht ganz so viel Sinn sehen die Mitarbeiter in den so genannten Shopfloors. Das oberste Gebot dort heißt Transparenz. Immer montags treffen sich zum Beispiel die Auftragsmanager. Jeder Teilnehmer muss vor dem Treffen das Shopfloor-Board aktualisieren. Das Ergebnis ist dann für alle Mitarbeiter sichtbar. Auf einer weißen Wand mit farbigen Magneten veranschaulicht. Grün ist gut, denn Grün heißt, alles läuft. Rot dagegen ist schlecht, denn Rot bedeutet, die Deadline wird nicht eingehalten, weil zum Beispiel ein Lieferteil fehlt.
"Man kann sich ja vorstellen, was das mit einem Menschen macht. Man kann zwar nichts dafür, wird aber trotzdem dafür verantwortlich gemacht. Was macht das mit einem Menschen? Das ist ein Ohnmachtsgefühl. Er wird da zwar nicht persönlich als Mensch angegriffen, er kann ja nichts dafür, aber er wird verantwortlich dafür gemacht."
"In unserem Unternehmen fing man mit Lean in der Produktion an und das war anfangs schon etwas kurios. Man fing in den Werkstätten damit an, erst einmal aufzuräumen. Man hat Linien auf den Boden gemalt. Das alles erinnerte uns erst einmal an ‚Schöner Wohnen‘. Doch durch das Aufräumen, dass die Werkzeuge immer am gleichen Platz sind, kam dann doch relativ schnell die Erkenntnis, in Lean steckt auch Sinn. Es hilft, produktiver zu werden und nicht so viel Zeit fürs Suchen zu verschwenden."
Nicht ganz so viel Sinn sehen die Mitarbeiter in den so genannten Shopfloors. Das oberste Gebot dort heißt Transparenz. Immer montags treffen sich zum Beispiel die Auftragsmanager. Jeder Teilnehmer muss vor dem Treffen das Shopfloor-Board aktualisieren. Das Ergebnis ist dann für alle Mitarbeiter sichtbar. Auf einer weißen Wand mit farbigen Magneten veranschaulicht. Grün ist gut, denn Grün heißt, alles läuft. Rot dagegen ist schlecht, denn Rot bedeutet, die Deadline wird nicht eingehalten, weil zum Beispiel ein Lieferteil fehlt.
"Man kann sich ja vorstellen, was das mit einem Menschen macht. Man kann zwar nichts dafür, wird aber trotzdem dafür verantwortlich gemacht. Was macht das mit einem Menschen? Das ist ein Ohnmachtsgefühl. Er wird da zwar nicht persönlich als Mensch angegriffen, er kann ja nichts dafür, aber er wird verantwortlich dafür gemacht."
Der Druck auf den Einzelnen steigt
Trotzdem hätten die transparenten Arbeitsprozesse auch Vorteile, betont der Betriebsrat. Die weißen Tafeln können bei der Fokussierung eines Problems helfen. Viele Abteilungschefs würden inzwischen realistischere Termine nennen. Und in der Fertigung laufen viele Prozesse effizienter. Bei manchen Produkten reduzierte sich die Durchlaufzeit sogar um die Hälfte. Er möchte Lean darum nicht verteufeln. Sein Unternehmen habe die Mitarbeiter geschult, ein Lean-Coach habe den Prozess anfangs begleitet. Niemand sei deswegen entlassen worden. Trotzdem bleibt er skeptisch.
"Der Druck auf den einzelnen steigt natürlich. Es ist ganz klar eine Arbeitsverdichtung. Das wird aber so natürlich nicht gesagt. Stattdessen wird gesagt, ja wir wollen eigentlich nur die unproduktiven Arbeitsprozesse effizienter machen. Das ist aber eine Milchmädchenrechnung. Wenn ich heute einen Prozess in 80 Prozent der Zeit erledigt kriege, dann brauche ich nicht mehr dieselbe Anzahl der Leute. Es sei denn, ich kann den Produktivitätsgewinn in mehr Produktion umwandeln. Das muss aber der Markt auch hergeben."
"Rechts und links sehen Sie ein paar Think Tanks, wo sich die Kollegen zurückziehen können, um Themen zu besprechen, und dahinter sind die einzelnen Projekträume."
Isabel Kalnik führt durch die Entwicklungsabteilung von Siemens. Links und rechts sieht man kleine, abgedunkelte Besprechungsnischen, wo zurzeit niemand sitzt. Da hinter seien die Großraumbüros, erläutert die Team-Leiterin für Lean-Kommunikation. Die Entwicklungsabteilung ist mit das Herzstück von Siemens. Hier dreht sich alles um den Kunden. Seine Wünsche, seine Anforderungen an ein Produkt. Die Ingenieure versuchen, sie so schnell und so gut wie möglich zu bedienen, um die optimalen Produkte zu entwickeln. Mit Erfolg, denn in diesem Jahr konnte der Erlanger Standort seinen Umsatz um 18 Prozent steigern.
"Der Druck auf den einzelnen steigt natürlich. Es ist ganz klar eine Arbeitsverdichtung. Das wird aber so natürlich nicht gesagt. Stattdessen wird gesagt, ja wir wollen eigentlich nur die unproduktiven Arbeitsprozesse effizienter machen. Das ist aber eine Milchmädchenrechnung. Wenn ich heute einen Prozess in 80 Prozent der Zeit erledigt kriege, dann brauche ich nicht mehr dieselbe Anzahl der Leute. Es sei denn, ich kann den Produktivitätsgewinn in mehr Produktion umwandeln. Das muss aber der Markt auch hergeben."
"Rechts und links sehen Sie ein paar Think Tanks, wo sich die Kollegen zurückziehen können, um Themen zu besprechen, und dahinter sind die einzelnen Projekträume."
Isabel Kalnik führt durch die Entwicklungsabteilung von Siemens. Links und rechts sieht man kleine, abgedunkelte Besprechungsnischen, wo zurzeit niemand sitzt. Da hinter seien die Großraumbüros, erläutert die Team-Leiterin für Lean-Kommunikation. Die Entwicklungsabteilung ist mit das Herzstück von Siemens. Hier dreht sich alles um den Kunden. Seine Wünsche, seine Anforderungen an ein Produkt. Die Ingenieure versuchen, sie so schnell und so gut wie möglich zu bedienen, um die optimalen Produkte zu entwickeln. Mit Erfolg, denn in diesem Jahr konnte der Erlanger Standort seinen Umsatz um 18 Prozent steigern.
"Dann gehen wir jetzt mal in den Triple O, den sogenannten Obeya of Obeya, Raum der Räume, wo wir für unsere Entwicklung unsere gesamten Projekte visualisieren und über die Probleme dort auch sprechen."
Isabell Kalnik hält ihre Chipkarte vor das Türschloss. Dahinter ein fensterloser Besprechungsraum. Nichts soll hier von den Problemen ablenken. Die vier Wände sind mit weißen Tafeln zugepflastert, auf denen rote, gelbe, grüne Magnete haften und unzählige weiße und rote Kärtchen und Zettel. Isabell Kalnik kommt ohne Umschweife auf die Farbe Rot zu sprechen.
"Sie sehen jetzt hier, wenn Sie die roten Karten betrachten, die Probleme, über die wir hier bei uns in der Entwicklung sprechen und die wir als Schätze betrachten. Denn nur, wenn wir sie kennen, können wir sie auch lösen."
Ganz oben auf den Whiteboards prangen Aufschriften wie "Projekteskalation", "Kundeneskalation", "IT-Probleme in work". Isabell Kalnik lächelt, sie kennt das. Nicht nur neugierige Journalisten, auch Kollegen stehen diesem Raum anfangs skeptisch gegenüber.
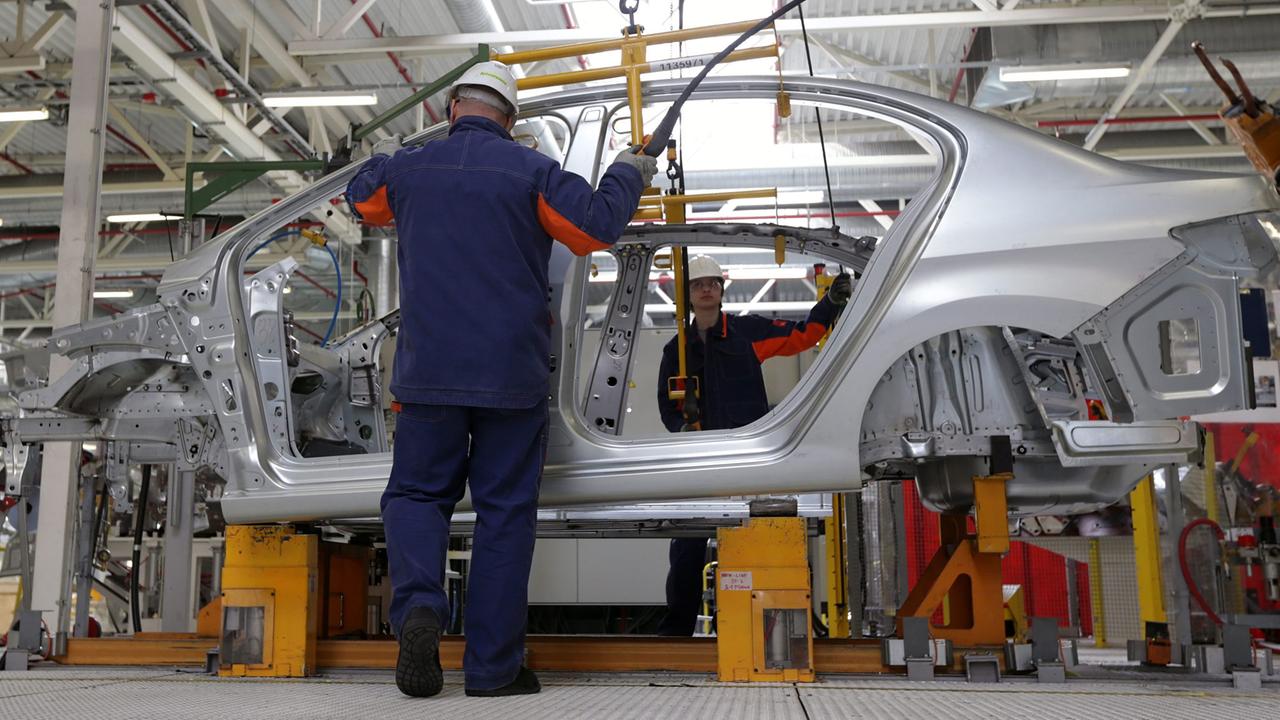
In der Autoproduktion ist die Lean-Production schon länger ein Begriff.© dpa / picture alliance
Ohne Transparenz und Wertschätzung geht es nicht
"Es ist nicht das Ziel, möglichst viele Zettel aufzuhängen, sondern das Ziel ist, sich hier gemeinsam auszutauschen. Einmal in der Woche, montags, von 12 bis 13 Uhr sind etwa 50 Personen in diesem Raum und zwar diejenigen, die Probleme haben und die Manager, die diese Probleme mitnehmen, um sie zu lösen. Das Besondere daran ist im Endeffekt der Kulturwandel. Dass man sich nicht versteckt, weil man ein Problem hat, sondern dass man die Transparenz hat und wertschätzend damit umgeht, um eben gemeinsam zu einer Lösung zu kommen."
Transparenz und Offenheit – alles für den Kunden. Vor Lean kam es immer wieder zu Konflikten: Die Kollegen vom Einkauf wollten günstig einkaufen, die Ingenieure das beste Produkt entwickeln. Jetzt wird der Kunde so früh wie möglich miteinbezogen.
"Das heißt, die Feedback-Kultur ist ganz wichtig, es ist ein Wandel der Kultur auch hier bei uns, die Art der Zusammenarbeit auf Vertrauensbasis einfach auch gemeinsam im Sinne des Kunden zu handeln."
Weil Zeit auch für Siemens Geld ist, beschränkt man die montäglichen Treffen auf eine Stunde. Auch das ist Lean. Abteilungsleiter mit einem roten Projektstatus haben also genau fünf Minuten, um ihr Problem zu veranschaulichen. Wer nicht fertig wird, ist in einer Woche wieder dran. Das Problem bleibt. Der psychische Stress sicherlich auch.
"Wir haben ein kleines Hilfsmittel, das hängt da vorne, also wir arbeiten mit einer Uhr, die aus der Ferne auch gut zu sehen ist. Man kann hier eben auf fünf Minuten stellen und wenn die Zeit dann rum ist, dann gibt´s piep, piep… und dann weiß jeder, er darf nicht mehr sprechen."
An der Wand gegenüber sind die laufenden Projekte aufgelistet. Auch hier verraten die Farben der Magneten den Status des Projekts. Bei Grün flutscht es, bei Gelb hat das Team Probleme, glaubt aber, sie in den Griff zu bekommen, und bei Rot eskaliert es. Für viele anfangs sicher eine ziemlich unangenehme, stressige Situation. Allein schon wegen des psychischen Drucks.
"Auf jeden Fall! Wir haben da ganz lustige Geschichten erlebt, dass eine Projektleiterin eben mit ihrer roten Karte rumgelaufen ist und versucht hat, die Karte einem Manager in die Hand zu geben und es war so ein richtiger Schreck, 'oh je, jetzt werde ich hier das Blaming bekommen, warum ich das Thema nicht gelöst habe'. Das ist tatsächlich nicht die Methode, es ist nicht die Vorgehensweise, es ist der Kulturwandel, der hier zählt. Es geht einfach darum, da wertschätzend miteinander umzugehen und das nicht als Blaming wahrzunehmen, sondern als gemeinsames Problem, was wir für den Kunden lösen wollen."
Transparenz und Offenheit – alles für den Kunden. Vor Lean kam es immer wieder zu Konflikten: Die Kollegen vom Einkauf wollten günstig einkaufen, die Ingenieure das beste Produkt entwickeln. Jetzt wird der Kunde so früh wie möglich miteinbezogen.
"Das heißt, die Feedback-Kultur ist ganz wichtig, es ist ein Wandel der Kultur auch hier bei uns, die Art der Zusammenarbeit auf Vertrauensbasis einfach auch gemeinsam im Sinne des Kunden zu handeln."
Weil Zeit auch für Siemens Geld ist, beschränkt man die montäglichen Treffen auf eine Stunde. Auch das ist Lean. Abteilungsleiter mit einem roten Projektstatus haben also genau fünf Minuten, um ihr Problem zu veranschaulichen. Wer nicht fertig wird, ist in einer Woche wieder dran. Das Problem bleibt. Der psychische Stress sicherlich auch.
"Wir haben ein kleines Hilfsmittel, das hängt da vorne, also wir arbeiten mit einer Uhr, die aus der Ferne auch gut zu sehen ist. Man kann hier eben auf fünf Minuten stellen und wenn die Zeit dann rum ist, dann gibt´s piep, piep… und dann weiß jeder, er darf nicht mehr sprechen."
An der Wand gegenüber sind die laufenden Projekte aufgelistet. Auch hier verraten die Farben der Magneten den Status des Projekts. Bei Grün flutscht es, bei Gelb hat das Team Probleme, glaubt aber, sie in den Griff zu bekommen, und bei Rot eskaliert es. Für viele anfangs sicher eine ziemlich unangenehme, stressige Situation. Allein schon wegen des psychischen Drucks.
"Auf jeden Fall! Wir haben da ganz lustige Geschichten erlebt, dass eine Projektleiterin eben mit ihrer roten Karte rumgelaufen ist und versucht hat, die Karte einem Manager in die Hand zu geben und es war so ein richtiger Schreck, 'oh je, jetzt werde ich hier das Blaming bekommen, warum ich das Thema nicht gelöst habe'. Das ist tatsächlich nicht die Methode, es ist nicht die Vorgehensweise, es ist der Kulturwandel, der hier zählt. Es geht einfach darum, da wertschätzend miteinander umzugehen und das nicht als Blaming wahrzunehmen, sondern als gemeinsames Problem, was wir für den Kunden lösen wollen."
Kein Kulturwandel ohne Coaching
Arbeitssoziologen wie Martin Kuhlmann betonen, dass dieser Kulturwandel nur durch umfangreiches Coaching möglich wird. Siemens hatte sich dafür Unterstützung aus Japan geholt. Der Spezialist begleitete die ersten Lean-Jahre in der Fertigung. Jeder Mitarbeiter wurde gecoacht. Für den Bereich Entwicklung wurde eigens eine Lean-Abteilung gegründet, die Isabell Kalnik leitet. 2000 Mitarbeiter mussten gecoacht werden. Um die Kollegen nicht zu überfordern, sei man nach dem Gaußschen Prinzip des kleinsten Zwangs vorgegangen, sagt Kalnik. Die Zeiten des vor sich hin wurschteln im stillen Kämmerlein sind jedenfalls vorbei. Entwickler, Tester, IT-Experten arbeiten in kleinen Teams zusammen, fühlen sich jetzt gemeinsam für das Produkt verantwortlich.
"Es ist eben nicht dieses: Ich mach´ nur mein Ding und habe nur meine Welt, sondern ich bekomme einen gesamten Blick auf das Projekt und es erweitert den Horizont und macht einfach Spaß, auf diese Art und Weise zusammenzuarbeiten."
Lean hat viele Vorteile. Produktionsprozesse werden verschlankt, Projekte transparenter gemacht, Fehler so schneller ausgemerzt. Es gibt aber auch Nachteile. Über die öffentlich zu reden, ist nicht einfach. Schließlich geht es um den eigenen Arbeitsplatz. Siemens-Mitarbeiter möchten darum nur anonym zu Wort kommen. Zum Beispiel über die gepriesene Teamarbeit in der Entwicklung.
"Früher saß man an mehreren Projekten und die Kolleginnen und Kollegen sind aufeinander zugegangen. Haben miteinander gesprochen, haben auch einmal in die andere Abteilung rüber geguckt. Und in den vielen Gesprächen einen ganz anderen Horizont bekommen, weil sie ja von den anderen Projekten auch was mitbekommen haben. Wo läuft denn was, was kann ich denn übernehmen. Wo ist denn was besser gelaufen. Jetzt bin ich halt nur noch in dem Projekt drin und kriege eigentlich von dem restlichen Umfeld ganz, ganz wenig mit."
In der Fertigung etablierte man 2012 die sogenannten Inseln mit mehreren Arbeitsplätzen. Bis zu sechs Mitarbeiter sitzen dort und jeder von ihnen muss den Job des anderen beherrschen. Da die Produktionsschritte aufeinander aufbauen, ist auch hier Teamarbeit gefragt. Das Ergebnis: Die Produktion konnte deutlich erhöht werden. Aber nicht immer zum Besseren des Einzelnen.
"Früher hatte jeder einen eigenen Arbeitsplatz, da konnte man sich ganz anders bewegen. Heute ist man viel abhängiger vom Kollegen, weil man in solch einer Insel ist. Vom Takt her. Wie schnell der Mitarbeiter vor einem ist, dementsprechend schnell muss oder kann man arbeiten. Dann kann man nur gemeinsam in die Pause gehen. Und wer mal kurz aufs Klo muss, fehlt dann in der Insel und seine Arbeit muss ein anderer mitmachen. Viele empfinden das als psychische Belastung. Und wegen der Prämienentlohnung möchte da auch niemand hinterherhinken, denn sonst wird man ganz schnell in der Gruppe nicht unbedingt gemobbt, aber doch negativ behandelt."
Er bezweifelt, dass ältere Kollege diesem Druck auf Dauer standhalten können. Trotz allem – die Stimmung in der Produktion ist seiner Ansicht nach gut. Auch wenn über jeder Insel ein LED-Bildschirm schwebt, der genau anzeigt, welches Gerät zu montieren ist, wie viele davon gut sind, wieviel Stillstand es gibt. Jede Sekunde kann man nachvollziehen, was gerade los ist. Auf der anderen Seite wurden in der Fertigung viele Qualifizierungsmaßnahmen durchgeführt. Manche Inseln werden jetzt von Mitarbeitern geleitet, die keiner Facharbeiter sind. Das System Lean schätzt auch menschliche Kompetenz. Und weil Fertigung und Versand dank Lean inzwischen so gut miteinander verzahnt sind, darf das Lager mit 140 Mitarbeitern in Erlangen bleiben und wird nicht wie an anderen Siemens-Standorten outgesourct. Selbst ein Prämienlohn habe seine Vorteile, meint ein Mitarbeiter und fügt dann hinzu, der Plan von oben sei glasklar: die Projekte schneller durchführen und das schaffe natürlich auch mehr Druck.
"Mit Lean wird die Arbeitsverdichtung massiv kommen, die Mitarbeiter werden noch schneller werden müssen, noch intelligenter arbeiten müssen und weniger soziale Kontakte pflegen können während der Arbeitszeit. Und unter sozialen Kontakten verstehe ich, auch mal ‘ne Tasse Kaffee trinken; es spricht ja hier keiner mehr über Fußball, sondern es wird nur noch über die Arbeit gesprochen."
"Es ist eben nicht dieses: Ich mach´ nur mein Ding und habe nur meine Welt, sondern ich bekomme einen gesamten Blick auf das Projekt und es erweitert den Horizont und macht einfach Spaß, auf diese Art und Weise zusammenzuarbeiten."
Lean hat viele Vorteile. Produktionsprozesse werden verschlankt, Projekte transparenter gemacht, Fehler so schneller ausgemerzt. Es gibt aber auch Nachteile. Über die öffentlich zu reden, ist nicht einfach. Schließlich geht es um den eigenen Arbeitsplatz. Siemens-Mitarbeiter möchten darum nur anonym zu Wort kommen. Zum Beispiel über die gepriesene Teamarbeit in der Entwicklung.
"Früher saß man an mehreren Projekten und die Kolleginnen und Kollegen sind aufeinander zugegangen. Haben miteinander gesprochen, haben auch einmal in die andere Abteilung rüber geguckt. Und in den vielen Gesprächen einen ganz anderen Horizont bekommen, weil sie ja von den anderen Projekten auch was mitbekommen haben. Wo läuft denn was, was kann ich denn übernehmen. Wo ist denn was besser gelaufen. Jetzt bin ich halt nur noch in dem Projekt drin und kriege eigentlich von dem restlichen Umfeld ganz, ganz wenig mit."
In der Fertigung etablierte man 2012 die sogenannten Inseln mit mehreren Arbeitsplätzen. Bis zu sechs Mitarbeiter sitzen dort und jeder von ihnen muss den Job des anderen beherrschen. Da die Produktionsschritte aufeinander aufbauen, ist auch hier Teamarbeit gefragt. Das Ergebnis: Die Produktion konnte deutlich erhöht werden. Aber nicht immer zum Besseren des Einzelnen.
"Früher hatte jeder einen eigenen Arbeitsplatz, da konnte man sich ganz anders bewegen. Heute ist man viel abhängiger vom Kollegen, weil man in solch einer Insel ist. Vom Takt her. Wie schnell der Mitarbeiter vor einem ist, dementsprechend schnell muss oder kann man arbeiten. Dann kann man nur gemeinsam in die Pause gehen. Und wer mal kurz aufs Klo muss, fehlt dann in der Insel und seine Arbeit muss ein anderer mitmachen. Viele empfinden das als psychische Belastung. Und wegen der Prämienentlohnung möchte da auch niemand hinterherhinken, denn sonst wird man ganz schnell in der Gruppe nicht unbedingt gemobbt, aber doch negativ behandelt."
Er bezweifelt, dass ältere Kollege diesem Druck auf Dauer standhalten können. Trotz allem – die Stimmung in der Produktion ist seiner Ansicht nach gut. Auch wenn über jeder Insel ein LED-Bildschirm schwebt, der genau anzeigt, welches Gerät zu montieren ist, wie viele davon gut sind, wieviel Stillstand es gibt. Jede Sekunde kann man nachvollziehen, was gerade los ist. Auf der anderen Seite wurden in der Fertigung viele Qualifizierungsmaßnahmen durchgeführt. Manche Inseln werden jetzt von Mitarbeitern geleitet, die keiner Facharbeiter sind. Das System Lean schätzt auch menschliche Kompetenz. Und weil Fertigung und Versand dank Lean inzwischen so gut miteinander verzahnt sind, darf das Lager mit 140 Mitarbeitern in Erlangen bleiben und wird nicht wie an anderen Siemens-Standorten outgesourct. Selbst ein Prämienlohn habe seine Vorteile, meint ein Mitarbeiter und fügt dann hinzu, der Plan von oben sei glasklar: die Projekte schneller durchführen und das schaffe natürlich auch mehr Druck.
"Mit Lean wird die Arbeitsverdichtung massiv kommen, die Mitarbeiter werden noch schneller werden müssen, noch intelligenter arbeiten müssen und weniger soziale Kontakte pflegen können während der Arbeitszeit. Und unter sozialen Kontakten verstehe ich, auch mal ‘ne Tasse Kaffee trinken; es spricht ja hier keiner mehr über Fußball, sondern es wird nur noch über die Arbeit gesprochen."
Bei vielen Firmen fehlt eine neue Unternehmenskultur
Was aber nicht am System Lean liege, sondern an der Art und Weise, wie Unternehmen diese Führungsphilosophie bei sich einsetzten, sagt Bettina Seibold. Die Sozialwissenschaftlerin und Ethnologin forscht dazu am Institut für Medienforschung und Urbanistik in Stuttgart. Diese Philosophie habe wesentliche Auswirkungen darauf, ob Mitarbeiter tatsächlich entlastet würden oder noch mehr Arbeit aufgebürdet bekämen. Im Auftrag der Hans-Böckler-Stiftung und der IG Metall Baden-Württemberg hat sie eine Studie erstellt. Mit dem Ergebnis, dass der Großteil der befragten Unternehmen Lean eher häppchenweise einsetzt.
"So ein konsequentes Gesamtkonzept, das ist nur in sehr wenigen Unternehmen zu finden. Was man häufig findet, sind einzelne Elemente, oder in einzelnen Abteilungen Elemente."
Elemente wie zum Beispiel die 5A Methode, mit der man seinen Arbeitsplatz aufräumt und die Dinge, die man braucht, sinnvoll sortiert. Oder Elemente wie die weißen Tafeln, auf denen die Entwicklung der Projekte mit farbigen Magneten gekennzeichnet wird. Die Einbeziehung der Mitarbeiter in diesen Prozess, sie als Experten ihrer Tätigkeit anzuerkennen und ihre Verbesserungsvorschläge ernst nehmen, dies passiere nur selten, sagt Bettina Seibold. Lean setzt eine andere Denkweise voraus. Eine neue Unternehmenskultur. Viele Unternehmen sind dazu nicht bereit. Zu groß sei der Verlust von Macht und Einfluss.
"In der alten Welt gibt es eine klare Hierarchie. Ich habe ein Team, ich habe eine Gruppe, ich habe eine Abteilung für die ich verantwortlich bin. Und durch dieses Lean sollen die Prozesse ja so optimiert werden, dass sich der Prozess quasi selbst steuert. Ich muss gar nicht mehr meine Leute kontrollieren, was die machen, sondern ich schaue auf den Prozess und dazu brauche ich dann auch weniger Führungskräfte. Wenn ich jetzt so ein konsequentes System habe, in dem jeder Fehler sichtbar wird und transparent, dann sieht man ja auch Schwächen und Stärken von Führungskräften."
"So ein konsequentes Gesamtkonzept, das ist nur in sehr wenigen Unternehmen zu finden. Was man häufig findet, sind einzelne Elemente, oder in einzelnen Abteilungen Elemente."
Elemente wie zum Beispiel die 5A Methode, mit der man seinen Arbeitsplatz aufräumt und die Dinge, die man braucht, sinnvoll sortiert. Oder Elemente wie die weißen Tafeln, auf denen die Entwicklung der Projekte mit farbigen Magneten gekennzeichnet wird. Die Einbeziehung der Mitarbeiter in diesen Prozess, sie als Experten ihrer Tätigkeit anzuerkennen und ihre Verbesserungsvorschläge ernst nehmen, dies passiere nur selten, sagt Bettina Seibold. Lean setzt eine andere Denkweise voraus. Eine neue Unternehmenskultur. Viele Unternehmen sind dazu nicht bereit. Zu groß sei der Verlust von Macht und Einfluss.
"In der alten Welt gibt es eine klare Hierarchie. Ich habe ein Team, ich habe eine Gruppe, ich habe eine Abteilung für die ich verantwortlich bin. Und durch dieses Lean sollen die Prozesse ja so optimiert werden, dass sich der Prozess quasi selbst steuert. Ich muss gar nicht mehr meine Leute kontrollieren, was die machen, sondern ich schaue auf den Prozess und dazu brauche ich dann auch weniger Führungskräfte. Wenn ich jetzt so ein konsequentes System habe, in dem jeder Fehler sichtbar wird und transparent, dann sieht man ja auch Schwächen und Stärken von Führungskräften."
Das Know-how der Mitarbeiter nutzen
Solch eine Führungskraft ist Hartmut Hoffmann ganz sicher nicht. Eher ein sympathischer Querdenker.
"Ich bin weder allwissend noch kann ich alles alleine machen. Der Tag hat nur 24 Stunden. Also muss ich gucken, dass das Know-how, das ist ja in vielen Unternehmen vorhanden, dass wir das Know-how der Mitarbeiter nutzen können. Aber sie nicht nur formal fragen, sondern wirklich fragen und sie berücksichtigen."
Hoffmann meint, was er sagt. Der 64-Jährige muss sich nichts mehr beweisen. Der gelernte Elektromechaniker und studierte Feinwerktechniker war Konstrukteur und Projektleiter im Bereich Luft- und Raumfahrt, hat mit am Eurofighter getüftelt und leitete danach mehrere Unternehmen. Als er vor zehn Jahren den Geschäftsleiterposten bei Rose & Krieger übernahm, war die Arbeitswelt noch in Ordnung, die Auftragsbücher voll. Das mittelständische Unternehmen stellt Komponenten und Module für die Automatisierungstechnik her, zum Beispiel für höhenverstellbare Arbeitsplätze. Doch ein Jahr später geriet das Mindener Unternehmen in den Strudel der weltweiten Wirtschaftskrise. Hartmut Hoffmann nutzte die Gunst der Stunde. Um verkrusteten Strukturen aufzubrechen, führte er die japanische Managementmethode Lean ein. Um sie erfolgreich zu etablieren, brauche es vor allem eins, sagt Hoffmann.
"Ich muss bereit sein, den Leuten Vertrauen zu geben. Wenn ich das nicht mache, wenn ich das nicht will, dann sollte ich das ganze Thema besser gar nicht anfangen. Das macht keinen Sinn. Diese Kultur muss von oben herab gelebt werden."
Nach dem Vertrauensbeweis kamen die Aufräumarbeiten. Im Büro und in der Produktion. Danach die Innovation. Welche Prozesse müssen verbessert, verschlankt werden. Schritt für Schritt ging man vor. Schulte machte eine Kollegin zur Lean-Expertin. Bezog die Mitarbeiter in den Prozess mit ein und schulte auch sie. Und noch etwas machte Hartmut Hoffmann richtig. Er gab Lean eine Chance.
"Was aus meiner Sicht sehr, sehr häufig vergessen wird, ist der Zeitfaktor. Wenn ich Menschen verändern möchte, eine Kultur eines Unternehmens verändern möchte, brauche ich nicht glauben, dass ich das innerhalb von einem halben oder einem Jahr geschafft habe."
Inzwischen ist Lean hier Routine. Es gibt 23 Teams, die sich regelmäßig treffen und austauschen. Im Vertrieb, im Büro, in der Fertigung.
"Also, ich würde vorschlagen ihr kommt alle wieder ein bisschen näher ran, damit ich nicht so laut werden muss. Und ihr ein bisschen mehr mitkriegt und mehr hört."
"Ich bin weder allwissend noch kann ich alles alleine machen. Der Tag hat nur 24 Stunden. Also muss ich gucken, dass das Know-how, das ist ja in vielen Unternehmen vorhanden, dass wir das Know-how der Mitarbeiter nutzen können. Aber sie nicht nur formal fragen, sondern wirklich fragen und sie berücksichtigen."
Hoffmann meint, was er sagt. Der 64-Jährige muss sich nichts mehr beweisen. Der gelernte Elektromechaniker und studierte Feinwerktechniker war Konstrukteur und Projektleiter im Bereich Luft- und Raumfahrt, hat mit am Eurofighter getüftelt und leitete danach mehrere Unternehmen. Als er vor zehn Jahren den Geschäftsleiterposten bei Rose & Krieger übernahm, war die Arbeitswelt noch in Ordnung, die Auftragsbücher voll. Das mittelständische Unternehmen stellt Komponenten und Module für die Automatisierungstechnik her, zum Beispiel für höhenverstellbare Arbeitsplätze. Doch ein Jahr später geriet das Mindener Unternehmen in den Strudel der weltweiten Wirtschaftskrise. Hartmut Hoffmann nutzte die Gunst der Stunde. Um verkrusteten Strukturen aufzubrechen, führte er die japanische Managementmethode Lean ein. Um sie erfolgreich zu etablieren, brauche es vor allem eins, sagt Hoffmann.
"Ich muss bereit sein, den Leuten Vertrauen zu geben. Wenn ich das nicht mache, wenn ich das nicht will, dann sollte ich das ganze Thema besser gar nicht anfangen. Das macht keinen Sinn. Diese Kultur muss von oben herab gelebt werden."
Nach dem Vertrauensbeweis kamen die Aufräumarbeiten. Im Büro und in der Produktion. Danach die Innovation. Welche Prozesse müssen verbessert, verschlankt werden. Schritt für Schritt ging man vor. Schulte machte eine Kollegin zur Lean-Expertin. Bezog die Mitarbeiter in den Prozess mit ein und schulte auch sie. Und noch etwas machte Hartmut Hoffmann richtig. Er gab Lean eine Chance.
"Was aus meiner Sicht sehr, sehr häufig vergessen wird, ist der Zeitfaktor. Wenn ich Menschen verändern möchte, eine Kultur eines Unternehmens verändern möchte, brauche ich nicht glauben, dass ich das innerhalb von einem halben oder einem Jahr geschafft habe."
Inzwischen ist Lean hier Routine. Es gibt 23 Teams, die sich regelmäßig treffen und austauschen. Im Vertrieb, im Büro, in der Fertigung.
"Also, ich würde vorschlagen ihr kommt alle wieder ein bisschen näher ran, damit ich nicht so laut werden muss. Und ihr ein bisschen mehr mitkriegt und mehr hört."
Ziel: ein reibungsloser Workflow
Jörg Schunke scharrt seine Mitarbeiterinnen und Mitarbeiter um sich. Ideenschmiede nennt der Leiter der Logistikabteilung das regelmäßige Treffen. Auf den Tafeln mit den weißen, gelben und roten Karten steht in großen Buchstaben: Plan, do, check, act. Schritt eins: Die Mitarbeiter analysieren, was wie verbessert werden muss. Schritt zwei: Den Plan in die Tat umsetzen. Schritt drei: Überprüfen, ob das auch erfolgreich ist. Und Schritt vier: Wenn ja, dann das nächste Thema in Angriff nehmen, wenn nicht, alles wieder auf Anfang. In dieser Reihenfolge.
Schunke berichtet stolz von der Monatsauswertung. Das Team sei gelobt worden für seine jüngsten Vorschläge, wie das Arbeiten in der Logistik noch effizienter wird. Denn darum geht es ja, um einen reibungslosen Workflow.
"Das wurde hier zwei Mal lobend erwähnt, von daher super Sache. Wenn ihr das auf dem Niveau so weiter macht, könnt ihr euch gegenseitig auf die Schulter klopfen, dann können wir ein tolles Ergebnis am Ende des Jahres abliefern… Ja, nichtsdestotrotz haben wir trotzdem ein paar Fehler gemacht. So ganz ohne ging es dann doch nicht. Und da sprechen wir jetzt einmal drüber."
Fehler seien da, um aus ihnen zu lernen und Probleme, um sie zu lösen, sagt einer der Mitarbeiter und lächelt dabei entspannt. Angst klingt anders. Bernd Wassermann, Facharbeiter für Logistik, hat den Lean-Prozess von Anfang an mitgemacht. Alles fing an mit dem 5A Prinzip. Das habe er anfangs belächelt, gibt der 52-Jährige offenherzig zu. Inzwischen schätzt er das Prinzip Ordnung. Und noch mehr das Prinzip Einmischung.
"Jetzt haben wir ja mitbekommen, dass viele Sachen, sage ich mal, da kann man mit reinsprechen. Einige Sachen könne wir erledigen, von uns aus, und das ist ja was eben jetzt, glaube ich, vielen Leuten guttut; und wo viele Leute vorher sagten, na ja, mal gucken, was das wird. Aber jetzt man kann Sachen selber umsetzen. Man hat einen gewissen Freiraum dadurch auch und das ist das Gute."
Früher wurschtelte jeder so vor sich hin, sagt Wassermann. Jetzt entscheide das Team über die Verbesserungsvorschläge und nicht der Chef. Aus dem Nebeneinander wurde ein Miteinander. Aus der effizienteren Arbeit aber keine Mehrarbeit, meint sein Kollege.
"Nö, es vereinfacht ja die Arbeit. Man ist abends nicht mehr so kaputt, wenn wir jetzt dieses Gestell zum Beispiel nicht hätten, dann müsste man sich immer bücken, immer im Kreis gehen. Kopf nach unten ist nicht so schön. So geht man in fast gerader Haltung und man schont auch so seinen Körper ein bisschen."
Besonders stolz ist Jörg Schunke auf den neuen Packplatz. In akribischer Kleinarbeit entwickelt er ihn mit Kollegen. Die Vorlage war ein Pappmodell. Das spare Kosten, sagt er. Auch ein Lean-Ansatz.
Schunke berichtet stolz von der Monatsauswertung. Das Team sei gelobt worden für seine jüngsten Vorschläge, wie das Arbeiten in der Logistik noch effizienter wird. Denn darum geht es ja, um einen reibungslosen Workflow.
"Das wurde hier zwei Mal lobend erwähnt, von daher super Sache. Wenn ihr das auf dem Niveau so weiter macht, könnt ihr euch gegenseitig auf die Schulter klopfen, dann können wir ein tolles Ergebnis am Ende des Jahres abliefern… Ja, nichtsdestotrotz haben wir trotzdem ein paar Fehler gemacht. So ganz ohne ging es dann doch nicht. Und da sprechen wir jetzt einmal drüber."
Fehler seien da, um aus ihnen zu lernen und Probleme, um sie zu lösen, sagt einer der Mitarbeiter und lächelt dabei entspannt. Angst klingt anders. Bernd Wassermann, Facharbeiter für Logistik, hat den Lean-Prozess von Anfang an mitgemacht. Alles fing an mit dem 5A Prinzip. Das habe er anfangs belächelt, gibt der 52-Jährige offenherzig zu. Inzwischen schätzt er das Prinzip Ordnung. Und noch mehr das Prinzip Einmischung.
"Jetzt haben wir ja mitbekommen, dass viele Sachen, sage ich mal, da kann man mit reinsprechen. Einige Sachen könne wir erledigen, von uns aus, und das ist ja was eben jetzt, glaube ich, vielen Leuten guttut; und wo viele Leute vorher sagten, na ja, mal gucken, was das wird. Aber jetzt man kann Sachen selber umsetzen. Man hat einen gewissen Freiraum dadurch auch und das ist das Gute."
Früher wurschtelte jeder so vor sich hin, sagt Wassermann. Jetzt entscheide das Team über die Verbesserungsvorschläge und nicht der Chef. Aus dem Nebeneinander wurde ein Miteinander. Aus der effizienteren Arbeit aber keine Mehrarbeit, meint sein Kollege.
"Nö, es vereinfacht ja die Arbeit. Man ist abends nicht mehr so kaputt, wenn wir jetzt dieses Gestell zum Beispiel nicht hätten, dann müsste man sich immer bücken, immer im Kreis gehen. Kopf nach unten ist nicht so schön. So geht man in fast gerader Haltung und man schont auch so seinen Körper ein bisschen."
Besonders stolz ist Jörg Schunke auf den neuen Packplatz. In akribischer Kleinarbeit entwickelt er ihn mit Kollegen. Die Vorlage war ein Pappmodell. Das spare Kosten, sagt er. Auch ein Lean-Ansatz.
Zufriedene Beschäftigte sind seltener krank
"Durch die Halle stand quer so eine lange Werkbank und dahinter saßen die Damen von der Montage. Und dann wurde das Material von da drüben auf den Packplatz geschoben und wurde verpackt, den Mitarbeitern in den Rücken geschoben …"
Sie rechneten akribisch nach: Am Tag musste sich jeder Verpacker mindestens 180 Mal drehen und bücken. Der modifizierte Packtisch verbesserte nicht nur die Ergonomie, er minimierte auch den Aufwand – um 40 Prozent. Was früher an mehreren Tischen stattfand, wird heute nur noch an einem Arbeitsplatz erledigt. Und was macht man mit der eingesparten Zeit? Noch mehr Produkte einpacken, sprich die Arbeit verdichten? Jörg Schunke schüttelt den Kopf.
"Das, was Sie gerade beschrieben haben, das hatte man am alten Packplatz. Wir mussten das Ganze rausholen, indem wir Mehrarbeit geleistet haben. Und dadurch, dass wir jetzt alles angepasst haben, fällt diese Mehrarbeit bei den Mitarbeitern nicht mehr an. Wir sind deutlich schneller geworden, so dass wir gar keinen Materialstau mehr haben, den wir mit Mehrarbeit wieder rausholen müssen. Und somit ist genau das Gegenteil erfolgt. Wenn die Arbeit weg ist, dann gehen die auch nach Hause."
Für ihn ist Lean das bessere Arbeitsmodell. Die Stimmung unter den Kollegen ist prima. Die Krankheitsquote, die sie hier scherzhaft Gesundheitsquote nennen, liegt unterm Durchschnitt. Und der Umsatz wächst. Selbst bei der Nachwuchssuche gibt es bislang keine Probleme. Und so hat der Besucher am Ende fast das Gefühl: Lean – oh, du schöne, neue Arbeitswelt.
Sie rechneten akribisch nach: Am Tag musste sich jeder Verpacker mindestens 180 Mal drehen und bücken. Der modifizierte Packtisch verbesserte nicht nur die Ergonomie, er minimierte auch den Aufwand – um 40 Prozent. Was früher an mehreren Tischen stattfand, wird heute nur noch an einem Arbeitsplatz erledigt. Und was macht man mit der eingesparten Zeit? Noch mehr Produkte einpacken, sprich die Arbeit verdichten? Jörg Schunke schüttelt den Kopf.
"Das, was Sie gerade beschrieben haben, das hatte man am alten Packplatz. Wir mussten das Ganze rausholen, indem wir Mehrarbeit geleistet haben. Und dadurch, dass wir jetzt alles angepasst haben, fällt diese Mehrarbeit bei den Mitarbeitern nicht mehr an. Wir sind deutlich schneller geworden, so dass wir gar keinen Materialstau mehr haben, den wir mit Mehrarbeit wieder rausholen müssen. Und somit ist genau das Gegenteil erfolgt. Wenn die Arbeit weg ist, dann gehen die auch nach Hause."
Für ihn ist Lean das bessere Arbeitsmodell. Die Stimmung unter den Kollegen ist prima. Die Krankheitsquote, die sie hier scherzhaft Gesundheitsquote nennen, liegt unterm Durchschnitt. Und der Umsatz wächst. Selbst bei der Nachwuchssuche gibt es bislang keine Probleme. Und so hat der Besucher am Ende fast das Gefühl: Lean – oh, du schöne, neue Arbeitswelt.